11 Best Practices In Industrial Packaging
6 Mins Read
Published on: 13 March 2023
Last Updated on: 05 May 2023
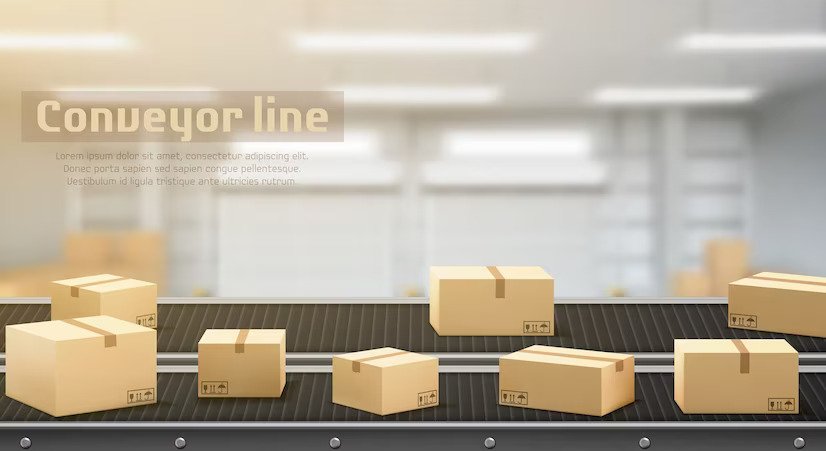
toc impalement
Industrial packaging is a critical aspect of the manufacturing and distribution industry. It refers to the procedures used to wrap, enclose, and seal finished industrial goods.
It involves the designing and development of packaging materials that can protect goods from external elements like moisture, temperature, and physical damage. Effective industrial packaging ensures that products reach their destination safely and securely.
Using suitable materials and designs, industrial packaging can shield products from impurities such as dirt, moisture, or chemicals. It can also safeguard items from potential damages during transportation and delivery while providing an aesthetically pleasing label and overall appearance to attract customers.
Since industrial packaging is used for various products, it’s vital to customize packaging materials to fit each unique item. Selecting materials tailored to the product in question helps ensure optimal protection against contaminants and damages.
Here Are 11 Best Practices In Industrial Packaging
That said, the following are some of the best practices in industrial packaging:
1. Tailored Packaging Solutions
Industrial packaging is undoubtedly the sector that stands out when meeting stringent packaging demands. The packaging solution should be tailored to fit the specific product needs it protects.
Whether for chemicals requiring such packaging, products requiring bulk bags, or large boxes. Different products have varying packaging requirements, which makes it crucial to have customized packaging. For instance, a fragile item like glassware requires a packaging solution to prevent it from breaking during transportation.
The packaging needs of the industrial sector are distinct, necessitating a customized approach to address either legislative requirements or the exceptional characteristics of their products. Successfully improved storage space, logistics, and transportation for clients across diverse industries are achieved by implementing an appropriate industrial packaging solution.
2. Use Of High-Quality Materials
The quality of packaging material used should be of high quality to ensure durability and stability during transportation. Inferior materials can cause the package to break or damage the products, leading to financial losses. Using high-quality materials will help protect the product during transport, ensuring it gets to the customer safely.
3. Protective Packaging Design
Packaging safeguards products from various potential hazards, such as exposure to sunlight, rain, insects, dust, and other damaging factors. It is especially crucial in food packaging as these products may be vulnerable to spoilage, rotting, or damage during transportation or storage. Therefore, businesses should take appropriate measures to prevent such risks and ensure the product’s quality, quantity, and color are not compromised.
Moreover, this can be achieved by designing the packaging to provide adequate cushioning and support for the product. For instance, bubble wrap or foam sheets can help protect fragile products. A packaging solution that effectively shields products from all possible risks can be considered good packaging.
When dealing with fragile goods, this becomes especially crucial. In many cases, most consumers consider packaging material a significant factor in purchasing these products. Inadequate packaging that results in product damage can significantly decrease the likelihood of repeat purchases.
4. Sustainable Packaging
Sustainable packaging refers to the use of biodegradable, renewable, and eco-friendly materials, as well as the implementation of measures by businesses to minimize the negative impact of packaging and shipping on the environment. It reflects a brand’s stance on sourcing materials for packaging and the types of materials that are environmentally friendly.
Although using sustainable packaging materials has become a prevalent trend among brands, simply adopting such materials doesn’t guarantee a sustainable packaging practice.
To establish a sustainable packaging policy, it’s crucial to:
- Ensure that the packaging can provide ample protection to the product throughout the supply chain.
- Educate customers about appropriate disposal methods for the packaging materials.
- Implement an efficient system for the usage of materials.
- Encourage continuous cycling of materials and minimize degradation.
- Ensure that the packaging poses no risks to human health or the environment.
Sustainable packaging materials are sourced responsibly and don’t contain harmful chemicals or substances that can cause health risks. These materials are typically organic.
Examples of sustainable packaging materials include:
- Paper products
- Biodegradable packing peanuts
- Corrugated bubble wrap
- Packaging made from cornstarch
- Organic fabrics
- Packaging made from mushrooms
- Seaweed packaging
- Certain types of plastics
- Biodegradable polymers
Making sustainable and innovative packaging investments can enhance the company’s brand and bolster business. It conveys to customers that environmental concerns are a priority and demonstrates dedication to sustainability. Such investments can also serve as a marketing tool to boost visibility and customer loyalty, thus constituting a valuable long-term investment. With this, our story at SupremeX is one of innovation and sustainability, as we are proud to offer a range of eco-friendly packaging solutions that help reduce waste and promote a cleaner future for generations to come
5. Efficient Packaging
Efficient packaging helps businesses save on costs and optimize their operations. It can be achieved using lightweight packaging materials that take up minimal space and are easy to assemble. It helps reduce shipping costs and increase storage space, optimizing the business’s operations.
6. Clear Labeling
Clear labeling is essential for effective industrial packaging. The packaging should have clear labels indicating the contents, quantity, and handling instructions. It helps ensure that the product reaches the customer in the proper condition, and it also helps minimize the risk of mishandling.
7. Withstand Harsh Environments
Certain packaging materials, such as cartons for transporting produce, are specifically engineered to endure diverse weather conditions. Distinct varieties of food packaging are manufactured for varying climates and consistencies of the contents.
The transportation of food necessitates preservation to prevent contamination from other foods or environments containing bacteria, viruses, or poisons.
As a result, several factors can influence food quality and taste after prolonged storage. Therefore, selecting appropriate packaging is crucial to uphold the freshness of the contents for an extended duration.
8. Compliance With Industry Standards
Businesses should ensure that their packaging solutions comply with industry standards and regulations. It helps ensure that the product meets the necessary safety and quality standards. Compliance also helps minimize the risk of legal issues and reputational damage.
Adhering to industry or legal standards when packaging your product is crucial to ensure compliance with health and safety protocols. It is especially critical when dealing with potentially hazardous products.
9. Consistency In Packaging
Consistency in packaging helps businesses build a strong brand identity. The packaging should be consistent across all products to ensure customers can easily recognize the brand. It also allows companies to create a strong visual identity and stand out.
Additionally, adopting mono-materials for packaging enables consumers to dispose of all materials in the same location, increasing recycling rates, particularly for paper-based materials.
10. Quality Control
Quality control is essential in ensuring that the packaging meets the necessary standards. Businesses should have a robust quality control system to ensure that the packaging is consistent and meets the required standards. It helps minimize the risk of inadequate packaging and product recalls.
11. Continuous Improvement
Continuous improvement is crucial in industrial packaging. Businesses should always look for ways to improve their packaging solutions to ensure that they are optimized for efficiency, sustainability, and safety. Continuous improvement also helps businesses stay ahead of the competition and meet the evolving needs of their customers.
Conclusion
Industrial packaging best practices are essential for ensuring the safe and efficient transportation of goods. Implementing these practices can help companies reduce costs, improve environmental sustainability, and enhance customer reputation.
Some key elements of industrial packaging best practices include choosing suitable materials, designing packaging that meets specific product requirements, using sustainable packaging options, and ensuring compliance with regulatory requirements.
By prioritizing these practices, companies can protect their products during transit and contribute to a more sustainable future for the industry.
Read Also:
Comments Are Closed For This Article