Proven Manufacturing Strategies: How To Minimize Production Waste
4 Mins Read
Published on: 21 August 2023
Last Updated on: 16 July 2024
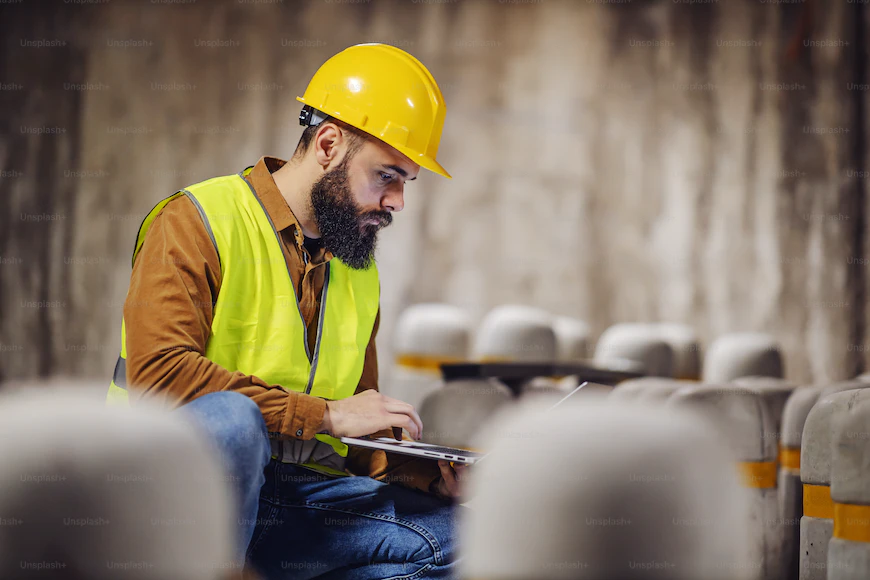
toc impalement
Production waste is one of the toughest challenges manufacturing businesses struggle with. Besides the cost of wastage, its environmental impact is a reason to worry. According to the Environmental Protection Agency, American industrial facilities are responsible for generating nearly 7.6 billion tons of solid waste each year. Despite the regulatory guidelines, the problem continues to persist.
Production waste management is a priority for manufacturers, with 8% of facilities initiating over 3,200 source reduction activities to minimize waste creation. Yet you may struggle as a factory owner due to a sheer lack of awareness regarding waste management practices.
Imagine the challenges of dealing with diverse issues, from excess raw materials to scrap, defective products, delays, and energy overuse. Things are even more challenging if your production unit uses toxic raw materials or generates similar end products because regulations may be tighter.
Fortunately, production waste management is easier than you imagine, provided you are ready to implement a few strategies from the outset. Here are a few proven methods to minimize your production waste.
Set A Realistic Waste Management Goal
In 2022, waste management services in the US made a whopping revenue of $140 billion after a decade of continuous growth. The number shows the country’s commitment to sustainability, and the industrial sector replicates the vision. As a manufacturer, you can take the first step by setting a realistic waste management goal.
Identify the areas of excess waste and develop a strategy to address them. Set measurable targets, such as cutting factory waste by 25% in the upcoming quarter. A plan enables you to quantify the progress toward the goal. It also helps you bring everyone in the factory on the same page and inspire them to work toward a common goal.
Adopt Process Innovation
Process innovation sets you up for minimizing production waste. Automation, for instance, can reduce production time and the possibility of human error. Not surprisingly, the global market for industrial automation products has grown at an exponential pace. It is estimated to cross the $178.10 billion mark by 2024. More than 14 million robots will be a part of industries by 2030.
Besides adopting process automation, consider switching to innovations such as CNC machining. The computer numeric control technology eliminates sub-surface damage and chipping. With every product moving out of the assembly line flawlessly, manufacturing companies can achieve a significant reduction in defective products.
According to Lattice Materials, CNC machining finds broad applications in industries such as defense, laser, commercial optics, and semiconductors. Greater accuracy and zero defects make this technology a worthy investment.
Practice Inventory Control
Recent surveys show that inventory worth over $163 billion is discarded each year due to overproduction or expiry. Food, pharmaceuticals, automotive, apparel, and beauty supply chains are the worst-hit verticals. Effective inventory control can resolve the issue, but eliminating excess stock is easier said than done.
Your workflows may necessitate maintaining certain levels of stock. However, overstocking can block your capital. Likewise, failure to track expiry dates can land you in trouble because a batch of expired raw materials can disrupt your production schedule and delay your orders. Create an effective inventory tracking system to manage inventory levels and use materials well before they go bad.
Set Up A Preventive Maintenance Schedule
Machinery breakdowns in factories are common, but they have a far-reaching impact. They can cause downtimes, manufacturing defects, and process delays, translating into high-volume production wastes. Your workers waste time, products may have flaws, and repairs lead to additional operating expenses.
According to estimates, Fortune Global 500 manufacturing firms lose 3.3 million hours annually to unplanned downtime. You can imagine the gravity of the issue from these numbers. A preventive maintenance schedule can be a savior as regular maintenance of industrial tools and machinery can prevent unexpected breakdowns and ensure uninterrupted production.
Think Sustainable
A sustainable approach aligns with waste management as it focuses on minimizing the use of resources and the production of waste in the manufacturing process. With 76.6% of emissions in the country driven by manufacturing production, sustainability also becomes an ethical responsibility for American manufacturers.
Consider the smart packaging move by Apple when the brand decided to ship its iPhones without the adapter to reduce the box size. Besides reducing packaging waste significantly, the change reportedly increased Apple’s profits by a staggering $6.5 billion.
Switching to energy-efficient machines, adopting smart appliances, and going solar are some other ways to set up a sustainable production process. All these steps automatically reduce manufacturing waste.
Closing Thoughts
Reducing factory waste saves money, promotes efficiency, and enhances your reputation as a manufacturer. The best part is that you can achieve waste minimization without a massive effort and investment. These actionable steps set you on the right track, and you can find more ways to be sustainable from there.
Read More:
Comments Are Closed For This Article