Safety In Construction Business: How To Protect Your Employees
5 Mins Read
Published on: 09 March 2024
Last Updated on: 10 March 2025
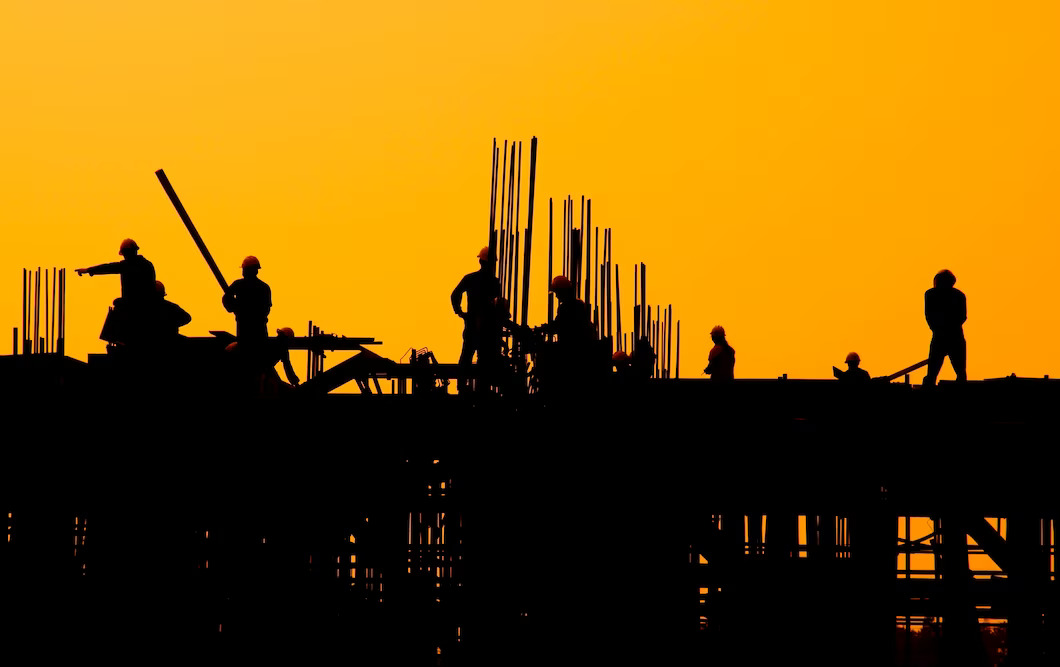
toc impalement
Construction sites are notorious for their dangerous work environments, including uneven surfaces, fall risks, heavy machinery, and outdoor weather hazards.
These hazards make roofing and construction the fourth and fifth most dangerous jobs, with around 20% of private industry worker fatalities in 2019.
Understanding these risks is crucial for mitigating accidents and promoting health and safety at construction worksites.
Moreover, construction workers are some of the most vulnerable employees. They can face workplace accidents, working with ladder-climbing, and using heavy machinery and dangerous tools.
Compared to people in other, easier professions, their rates of injury and death are three times higher.
In the contracting world, it takes hard work to build a business, and contractors are at greater risk for losses that could devastate a business.
Protecting livelihoods, employees, and assets requires understanding the hazards they face on the job every day.
Understanding The Laws Against Injuries In Construction Sites
New York State Labor Law 240 mandates that building owners and general contractors provide workers with proper safety equipment to prevent falls.
Construction attorneys and personal injury attorneys in Austin can help avoid costly mistakes. They help you bring strong cases by filing timely lawsuits, identifying liable parties, and pursuing claims against employers and non-employers.
They can conduct thorough investigations, gather evidence, and negotiate settlement offers from insurance companies, which may not always be in the injured worker’s best interest.
In summary, construction attorneys are essential in navigating construction lawsuits and obtaining compensation for injuries.
How To Ensure Employee Protection In Construction Business?
Given below are some important tips that will help you ensure protection for your employees in the construction business—
1. Make Your Employees Aware
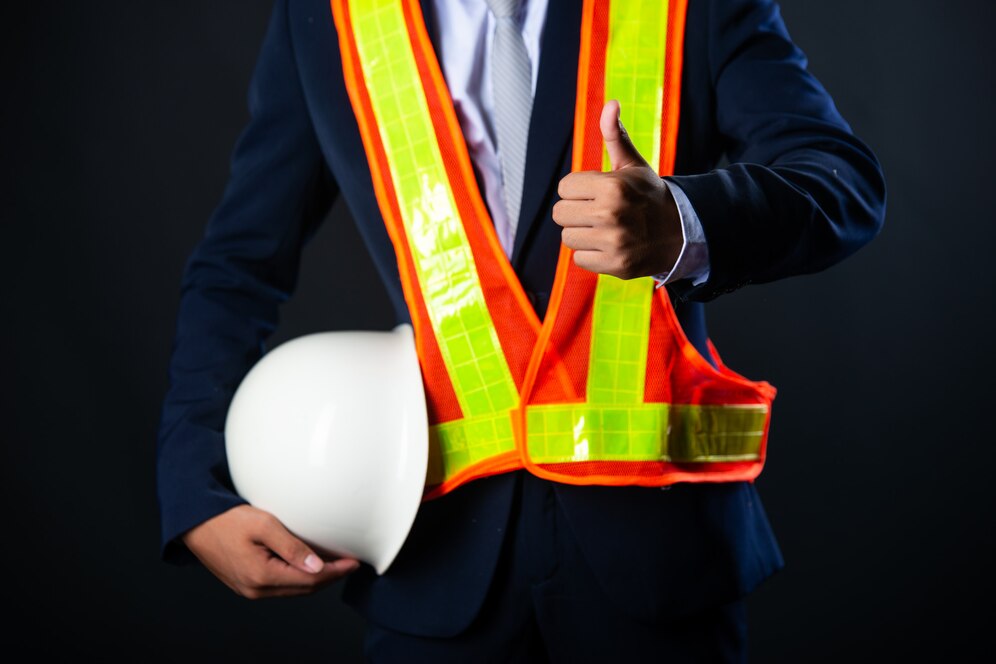
Teaching situational awareness to employees is a crucial safety precaution. This helps them spot potential hazards and safety issues before accidents occur.
Training employees in hazard identification and responding to them is essential. An untrained employee may not see an accident coming, while a trained employee might.
Encouraging workers to slow down and pay attention to their surroundings is crucial. Moreover, standard compliance training helps employees understand the daily hazards, making the job safer and protecting the company’s bottom line.
Communication is also crucial in keeping employees safe. Staff should communicate with each other and any alternative parties when identifying potential risks. You can shop two way radios to help ensure communication is transparent and easy.
Make your onsite workers aware of existing hazards and other dangers. Regularly asking employees about potential safety improvements and allowing them to report accidents or near-misses can help ensure a safer work environment.
2. Conduct Training
Employees need to have the necessary training to work safely. This includes job-specific training on power tools, first aid, and handling hazardous substances.
Employees should regularly take mandatory courses, such as biannually or quarterly, to ensure they can respond effectively in dangerous situations. Offering incentives can also keep employees engaged.
The NEBOSH Construction Certificate is a comprehensive Health and Safety course. It helps equip construction workers with the skills required for high and medium-risk environments.
Moreover, the course includes training on first aid, techniques, and procedures.
It ensures workers are aware of safety hazards and how to handle them, promoting a safer work environment. This course is particularly useful for workers in confined spaces, at height, or with machinery.
3. Install Signs
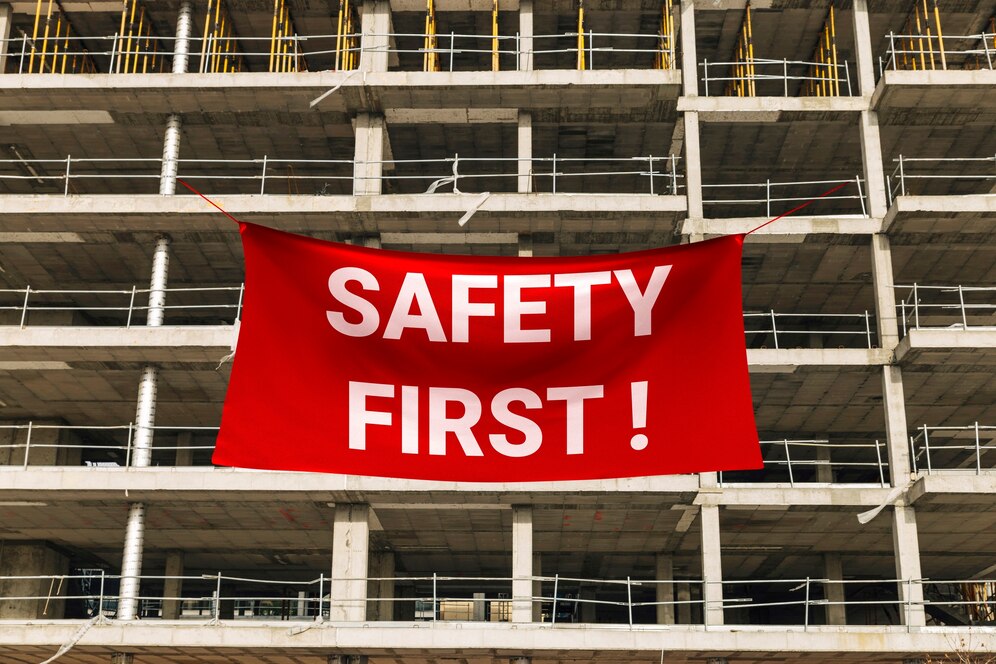
Construction sites can be hazardous, not just for the workers but for the general public as well. Therefore, it is crucial to take necessary precautions to avoid any accidents.
One of the cost-effective ways to reduce the likelihood of accidents is by displaying signs and posters highlighting potential hazards.
These signs could indicate various dangers, such as the risk of falling objects, large vehicles turning, or the presence of hazardous gas or chemicals.
Therefore, by displaying such signs, everyone in the vicinity can stay informed and be cautious, ensuring a safer working environment for all.
4. Use PPE & Safety Kits
It is important to provide workers with appropriate personal protective equipment (PPE) for any job that may pose a risk to health and safety.
According to OSHA regulations, you must provide PPE free of cost to your employees.
Furthermore, there are specific standards for what should be available, like the following:
- Hard hats.
- Safety goggles.
- Gloves.
- Hearing protection.
- Fall prevention harnesses.
- High-visibility clothing.
- Steel-toed boots.
It is crucial to keep equipment lists updated due to changing job sites and industry best practices.
It is essential to have a regular schedule for revisiting standard requirements, unique equipment needs for specific sites and occupations, and employee feedback to ensure security.
To ensure effective protection, it is necessary to maintain equipment quality and train employees on proper use.
In an emergency, a fully stocked on-site first aid kit should always be available, including band-aids, gauze pads, tape, and other necessary items.
5. Keep Assessing The Risks
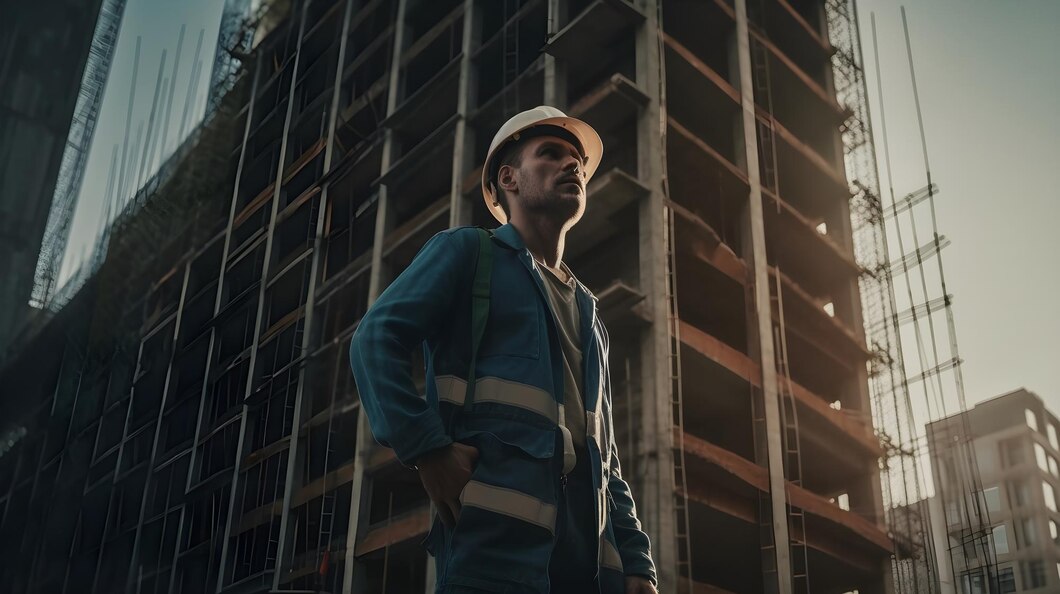
To ensure safety on the job site, it’s important to identify specific hazards and tailor safety efforts accordingly.
Conducting a risk assessment considering environmental factors such as weather, heat, and natural disasters is key to developing plans to mitigate risks and address employee responses.
Secure equipment, tools, building materials, and vehicles when not in use to prevent theft or vandalism.
Moreover, it is important to maintain records of equipment. Also, you can install fences, use theft deterrents like wheel and ignition locks, and consider investing in security cameras or guards.
Workers in the construction industry rely heavily on their tools to get the job done efficiently, and unsafe or broken tools increase the risk of serious accidents.
Regular equipment inspections are necessary to prevent malfunctions, and consulting with local law enforcement can help maintain a safe work environment.
Play It Safe!
Construction site safety is more than following OSHA safety standards or installing caution tape.
It involves instilling commitment and accountability in workers and creating a safe work environment. Arming employees with knowledge, training, and protective equipment prepares them for success.
Support from leadership and encouragement can lead to speed, efficiency, and cost savings.
Developing a building site safety checklist is an effective way to verify safety precautions. Each hazard on the job site deserves a checklist, reinforcing safe work practices and serving other purposes.
Checklists include inspecting tools, verifying PPE, and considering potential effects on the surrounding area. Also, you must document compliance with OSHA violation standards and provide safety tips for construction workers.
Read Also:
Comments Are Closed For This Article