Warehouse Efficiency: Streamlining Operations with Effective Rack Repair Strategies
5 Mins Read
3 comments
Published on: 21 May 2024
Last Updated on: 06 September 2024
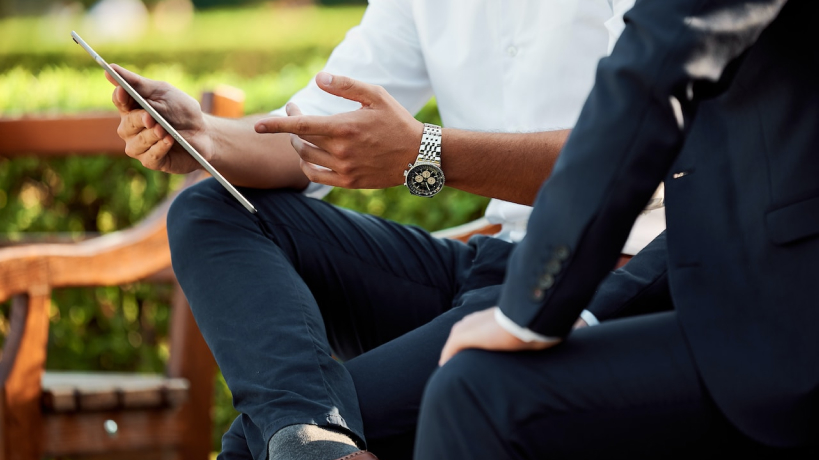
toc impalement
Key Takeaways:
- Understanding the role of rack repair in maintaining warehouse efficiency.
- Best practices for inspecting and repairing warehouse racks.
- The cost-benefit analysis of regular rack maintenance versus replacement.
Introduction
It’s a complex task that calls for proactive facility management and close attention to detail to maintain operational efficiency in storage. At the heart of this lies the need to ensure warehouse racking systems’ integrity and proper functioning.
In busy logistics centers like Columbus, Ohio, individuals tasked with maintaining warehouse efficiency recognize the importance of reliable racking and seek services from proficient technicians who know the intricacies of rack repair Columbus,Ohio.
Proper care of racking systems does more than prevent catastrophic failure; it plays a critical role in the seamless flow of operations, supports worker safety, and helps maintain inventory in excellent condition.
The Significance of Rack Integrity in Warehousing
A sturdy and well-designed warehouse rack system does more than hold commodities; it is integral in optimizing space and time management within a warehouse setting.
Ensuring these structures are in top condition is vital for preventing physical collapse and upholding the overall operational integrity of a warehousing environment. A warehouse that prides itself on operational efficiency recognizes that well-maintained racks ensure smooth access to products, accurate inventory tracking, and safe storage solutions.
Therefore, the racks’ structural integrity safeguards warehouse personnel’s wellness and the security of merchandise stored within.
Identifying Common Issues with Warehouse Racking Systems
Various factors contribute to the degradation of racking systems, including material fatigue, overloading, accidental forklift impacts, and environmental conditions, which may cause corrosion.
An eagle-eyed warehouse manager must constantly look for telltale signs of rack deterioration, such as abnormal bending, warping, or visible damages to the uprights and cross beams.
Early detection of these signs allows for timely intervention, staving off further damage and maintaining the operational cadence of warehousing activities. By addressing these issues promptly, warehouses avoid the escalated costs associated with rack replacement and the potential safety risks.
Regular Inspections: The First Line of Defense Against Rack Damage
Diligent inspections form a foundational practice in the preventive maintenance of racking systems. Establishing a systematic inspection strategy guarantees that all rack components, including load beams, braces, bolts, and anchors, continue functioning as intended.
As such, regular checks must be conducted by trained personnel capable of identifying the subtleties of rack damage. This approach is akin to conducting regular audits to maintain financial health—by keeping an eye on the finer details, potential oversights can be caught and rectified before they burgeon into costly overhauls.
Therefore, inspections are the first and most crucial line of defense in maintaining racking systems, preventing minor issues from escalating into extensive repairs or replacements.
DIY vs. Professional Rack Repair: Assessing the Best Approach
Deciding between an in-house repair team and enlisting professional services requires careful consideration of various aspects. While utilizing the warehouse staff to address minor damages may seem cost-efficient, the professionals’ expertise can prove indispensable, especially for more complex repairs.
Experts equipped with specific tools and current knowledge of the latest repair processes provide precision and attention to risks that the inexperienced eye would overlook.
Moreover, given the regulatory environment governing warehouse safety, professionals ensure that the repairs meet industry standards, thus mitigating the risk of non-compliance and related penalties.
Analyzing the Long-Term Benefits of Proactive Rack Maintenance
Investing in the upkeep of warehouse racking is akin to investing in the longevity of the warehousing operation as a whole. By conducting maintenance activities regularly, facilities can avert the need for large-scale repairs and replacements, which can be disruptive and expensive.
A well-planned maintenance regimen comprises scheduled inspections and immediate repair to damage and considers load management and reconfiguration needs as the warehousing demands evolve.
Over time, these proactive measures result in an incrementally safer work environment, saving the operation from substantial financial losses and potential downtimes.
Integrating Rack Repair Into a Lean Warehouse Management Strategy
A lean warehousing strategy is dedicated to reducing inefficiencies and eliminating waste in pursuit of a more streamlined operation. Within this framework, rack repair and maintenance play a crucial role.
Integrating a systematic repair program into a lean management philosophy ensures that every identified flaw is addressed promptly and efficiently, reducing wasted space, time, and resources.
When repair activities are incorporated seamlessly into the daily tasks of a lean operation, the warehouse can maintain an uninterrupted flow, which ultimately contributes to better service delivery and cost management.
Minimizing Downtime: Effective Scheduling for Rack Repairs
Strategically planning and effectuating repairs during periods that will cause the least disruption to warehouse operations is ideal. Orchestrating repair actions during quieter shifts or planned downtimes ensures that the productivity and workflow within the warehouse are maintained.
This level of strategic planning requires a solid understanding of the operation’s peak hours and the capability to mobilize repair teams swiftly. Efficiency in scheduling and executing repairs limits the impact on operational throughput and underscores a well-managed warehousing operation.
Adhering to Safety Standards in Rack Repair and Maintenance
Compliance with established safety standards and protocols has several benefits within a warehousing operation. It’s about adherence to legal requirements and creating a secure work environment.
Regular rack inspections and repairs should follow the guidelines set by OSHA and other safety organizations pertinent to the warehousing and logistics sectors.
This conscientious adherence ensures that all staff operates in a facility where risk is minimized and safety procedures are a routine part of maintaining the infrastructure.
Utilizing Technological Advancements in Rack Repair Solutions
The warehouse industry has quickly adopted innovative technologies that enhance the efficiency and efficacy of maintenance practices.
For instance, drones for aerial inspections of hard-to-reach areas can significantly reduce inspection times and improve safety. Additionally, using advanced materials for repairs, such as high-strength steel and clever welding techniques, can extend the life of repaired sections, delivering increased reliability.
Embracing such technological advancements can lead to a more responsive and effective maintenance protocol, which aligns perfectly with the evolving nature of modern warehousing operations.
Concluding Words: Implement a Rack Repair Program Today!
Illustrative examples from real-life scenarios often provide the most compelling evidence of the benefits wrought by a dedicated rack repair program.
Case studies from various warehouses document how an organized and carefully implemented rack repair strategy results in a safer work environment, enhanced operational flow, and improved cost management.
These examples highlight a common outcome: when warehouse infrastructure is consistently maintained, all operational processes benefit, thus driving the organization toward sustained efficiency and growth.
To gain a more profound understanding of effectively maximizing warehouse space and safety, one must comprehend the underlying principles of warehouse racking systems.
3 comments
real estate May 21, 2024 at 7:24 pm
Wow, superb blog format! How long have you been running a blog for? you make running a blog look easy. The entire glance of your site is wonderful, as smartly as the content material!
oelltd May 22, 2024 at 1:53 am
Excellent blog here! Also your web site loads up very fast! What host are you using? Can I get your affiliate link to your host? I wish my site loaded up as fast as yours lol
doomslot May 22, 2024 at 1:59 am
Good way of explaining, and nice article to get information on the topic of my presentation subject, which i am going to deliver in college.