Decoding the Logic: Maximizing Efficiency in Automated Manufacturing Systems
6 Mins Read
Published on: 14 July 2023
Last Updated on: 20 November 2024
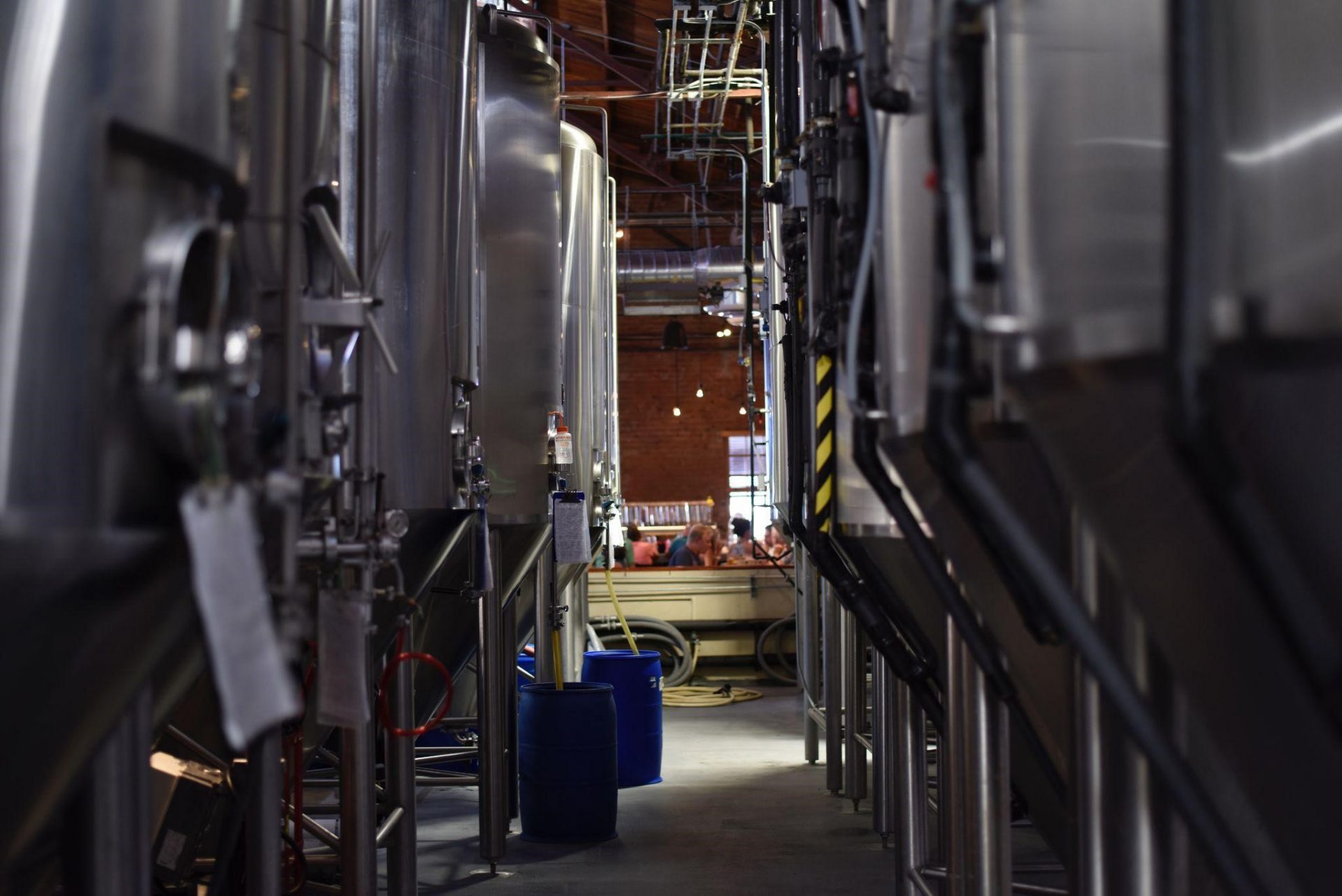
toc impalement
In the age of digitization and rapid technological advancements, one sector that has witnessed a significant transformation is manufacturing.
Automated manufacturing systems have now become a common occurrence, redefining efficiency and productivity levels across diverse industries.
This article seeks to decode the logic behind automation in manufacturing, highlighting various strategies for maximizing their efficiency.
What are Automated Manufacturing Systems?
Automated Manufacturing Systems (AMS) are technology-driven processes that employ automation tools and machinery to produce goods with minimal human intervention.
When viewed holistically, an AMS acts as an integrated system, converting raw materials into finished goods through a series of programmed instructions.
Types of Automation in Manufacturing
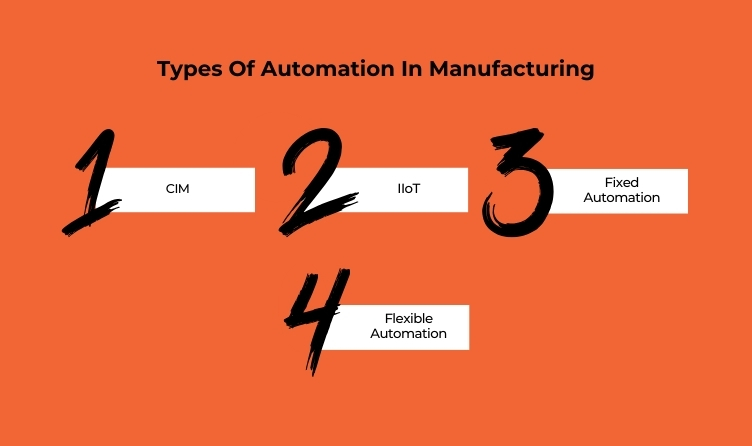
Automated manufacturing systems are all set to change the very landscape of business manufacturing.
In the upcoming years, automated manufacturing will become more robust with the help of AI. Therefore, it is high time for businesses to focus more on manufacturing automation systems.
But to make a successful switch, you need to first understand the different variants of manufacturing process automation that are out there.
CIM
Computer Integrated Manufacturing, or CIM, is a manufacturing process that is entirely dictated by automated machines or systems.
In a way, a CIM is a cluster of automated machines that is run by a single computer. This computer system monitors everything from production to quality control.
IIoT
IIoT, or Industrial Internet Of Things, is a considerable step up from CIM because IIoT automated manufacturing systems use AI to a great extent.
Therefore, IIoT manufacturing process automation minimizes the scope of human error and actually improves the quality of the manufacturing process.
Fixed Automation
Fixed or Hard automation machines refer to machines that are only supposed to work on one particular task. These machines usually come in pre-programmable formats.
You will not be able to change the very protocol of a fixed automation system. You will not be able to use the CNC cutter for anything else. However, that does not mean that the device is not useful in any way.
Flexible Automation
Flexible Automation is the absolute opposite of fixed automation. These automated systems come with a flexible programmable module. That allows flexible programming and usage.
This is usually found in small-scale industries that are focused on maximizing their equipment. However, a specialized machine is always better at its dedicated job than a ‘jack of all trades.’
Importance of Efficiency in AMS
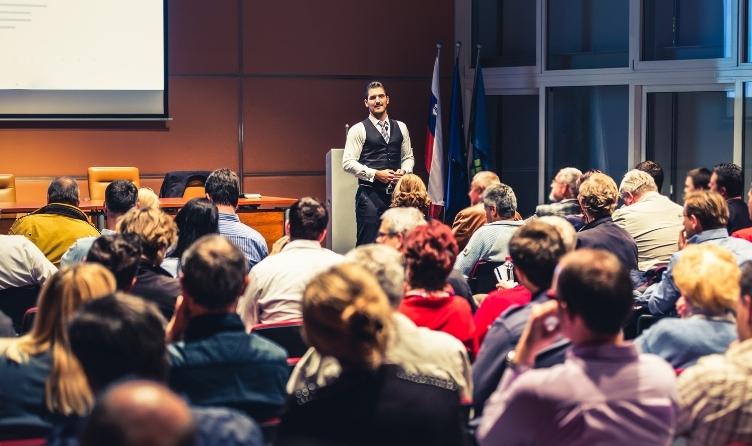
Efficiency in an AMS means accomplishing the maximum production output with the minimum input of resources, such as time, energy, and materials. An efficient AMS reduces waste, lowers production costs, and increases overall productivity. Additionally, higher efficiency means fewer errors and less downtime, which translates into improved reliability and customer satisfaction.
Techniques To Meet Critical Production Monitoring KPIs
Now that we’ve understood the essence of an AMS and why efficiency is vital, let’s delve into various strategies to maximize efficiency in an AMS.
- Process Optimization: Efficiency begins with optimizing each process in the manufacturing cycle. This involves:
- Eliminating Waste: Identify wasteful processes in the production cycle and eliminate them. Lean manufacturing and Six Sigma techniques are excellent methodologies for this.
- Reducing Cycle Times: By decreasing the time taken for each process, the total production time reduces, enhancing efficiency.
Advanced Technologies
Embracing advanced technologies can significantly increase AMS efficiency.
Artificial Intelligence (AI) and Machine Learning (ML): AI and ML can predict system failures, allowing for preventative maintenance, which increases system uptime. AI can also optimize production schedules to improve resource utilization.
- Internet of Things (IoT): IoT devices collect real-time data, which can be used to track system performance, predict equipment failures, and ensure quality control.
- Robotics: Robots offer accuracy, speed, and consistency. They can perform repetitive tasks more efficiently than humans, freeing the human workforce for more complex tasks.
Regular Maintenance
Regularly servicing and maintaining the machinery and tools used in the manufacturing process can reduce the downtime caused by machine failure, thus increasing the efficiency of the AMS.
Employee Training
While automated systems reduce human intervention, human control is still crucial. Employees need to be trained to handle new technologies and troubleshoot minor issues.
Continuous Monitoring and Improvement
Efficiency is not a one-time goal but an ongoing process. Hence, continuous monitoring and process improvement are critical. Track performance and identify areas for improvement using real-time data.
Components for Automated Manufacturing
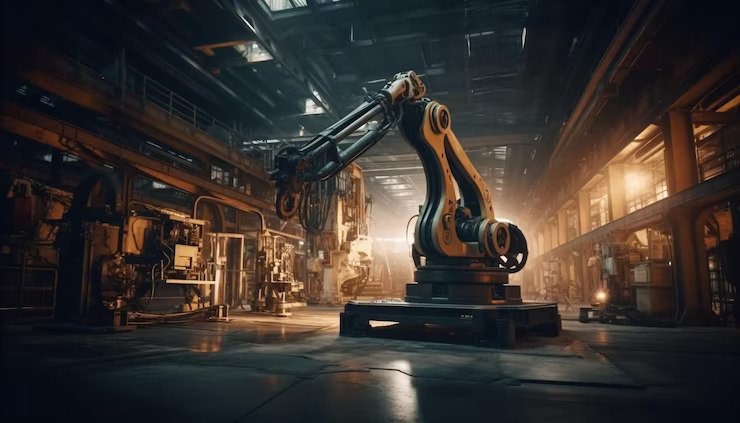
To optimize the performance of an AMS, understanding the key components and their role in enhancing efficiency is crucial.
Here are some vital parts to consider:
1. High-quality Hardware
The efficiency of an AMS is significantly reliant on the quality of the machinery and hardware used.
Machines with high precision, durability, and speed lead to less downtime, lower maintenance costs, and improved product quality.
Besides, integrating collaborative robots (cobots) can further improve efficiency by working in sync with humans to perform complex tasks.
To further emphasize the importance of high-quality hardware, it’s essential to consider the role of innovative and future-proof technology.
2. Cutting-edge Software
The right software enables seamless communication between different hardware components, thereby optimizing the entire process flow. Advanced Manufacturing Execution Systems (MES), for example, can track and document the transformation of raw materials to finished goods, enhancing transparency and control.
Moreover, the role of cutting-edge software extends beyond mere communication and process tracking. Modern automated manufacturing systems leverage advanced data analytics software to harness the wealth of data generated during the manufacturing process.
These software solutions can analyze operational data in real time, helping to identify bottlenecks, predict machine failures, and optimize resource allocation, thus increasing overall operational efficiency.
3. Compact PLCs and HMIs
A compact PLC, despite its small size, can effectively control large-scale industrial processes, providing a compact, cost-effective control solution. It is highly flexible and can adapt to various automation needs, leading to streamlined operations and improved efficiency.
Meanwhile, HMIs are a user-friendly interface between the operator and the AMS. They display data from the PLCs in an easily digestible format, allowing operators to monitor and control complex operations efficiently.
When considering purchasing Compact PLCs and HMIs, manufacturers employing automated industrial applications should look to leading suppliers such as Beijer Electronics. This company provides high-quality, compact, and cost-effective PLC solutions that are highly flexible, capable of adapting to various automation needs and leading to streamlined operations and improved efficiency.
4. Sensing and Inspection Systems
Sensors and inspection systems are critical for real-time data collection and quality control. They help prevent machine failure, reduce waste, and maintain the quality of the products.
Building on the foundational roles of sensing and inspection systems, modern technologies are expanding these functionalities even further. Adopting smart sensors and advanced inspection systems is propelling the manufacturing sector toward more predictive and proactive operations.
5. Connectivity Solutions
In today’s Industry 4.0 era, connectivity is key. Technologies like IoT allow for interconnectivity between machines, leading to a smarter and more synchronized manufacturing process. Additionally, cloud-based solutions can facilitate data storage and remote access, further improving efficiency.
Case Study: Toyota’s Just-In-Time Production
A successful application of efficiency in an AMS is Toyota’s Just-In-Time (JIT) production system. The JIT system aims to produce only what is needed when it’s needed and in the amount needed. This approach reduces waste, lowers costs, and improves efficiency by eliminating excess inventory and overproduction.
The Future of Efficiency in AMS
The future holds even more potential for efficiency in AMS, with technologies like 5G, quantum computing, and advanced robotics. The integration of these technologies will allow AMS to operate more interconnectivity, speedily, and precisely.
As we continue to innovate and create more advanced automated systems, the potential for efficiency and productivity will only grow. Remember, the goal is not merely to automate but to automate efficiently.
Read Also:
Comments Are Closed For This Article