Industrial Applications For Collaborative Robots
5 Mins Read
Published on: 29 June 2022
Last Updated on: 08 December 2022
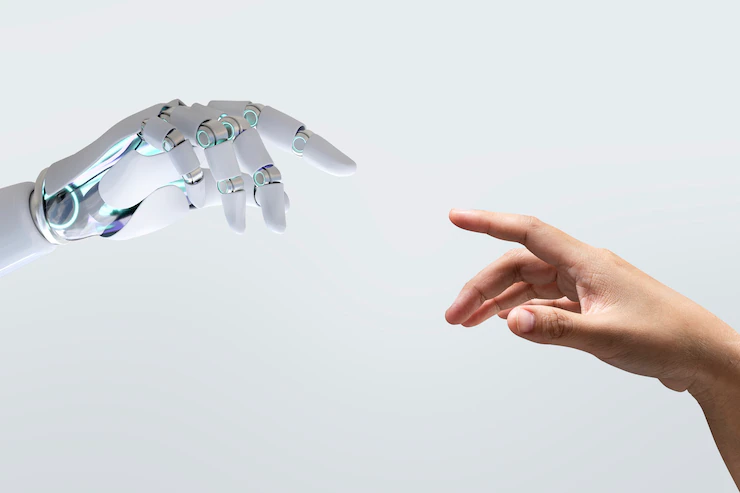
toc impalement
Several years ago, industrial use of robots was limited to selected areas of operations where the machines worked in enclosed spaces. However, advanced technology in robotics has rapidly increased the flexibility, versatility, and functionalities of robots in recent years.
Leading in these technological advancements are collaborative robots, also known as cobots. Cobots have several industrial applications. They are designed to work with humans in several areas of operation, including machine tending, material handling, and packaging.
Collision detection and force feedback are key cobot security features that allow collaboration with humans. Getting a collaborative robot for your company would improve your employees’ safety and increase the efficiency of production processes.
Let us now look at common industrial applications of collaborative robots.
Common Industrial Applications of Collaborative Robots
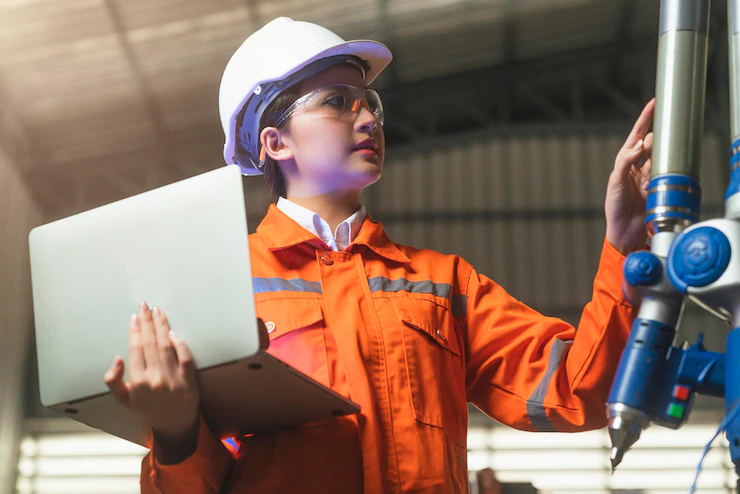
If you run a manufacturing industry, you have probably once experienced the challenge of producing high-quality goods while keeping prices low for your customers. Using robots in manufacturing could allow you to accomplish this goal and maintain a large profit margin.
1. Welding
One of the areas in manufacturing that have greatly benefited from cobots is welding and soldering. Although your human workers may perform these tasks to your satisfaction, they take too long to produce large volumes of goods.
Moreover, recent research by the American Welding Society shows that the shortage of welding professionals is expected to increase to 290,000 in the US. Hence to avoid this setback, many companies are adopting collaborative robots.
Although setting up cobots is expensive, the long-term benefits of using collaborative robots in welding are worth the investment. The cobots have computer vision and sensors that increase their ability to sense their proximity to humans.
These sensing capabilities allow the robots to notify workers about catastrophic environments to prevent work-related injuries or loss of lives.
Using cobots for welding activities ensures consistency in welding tasks. This consistency is difficult to achieve with human workers. Consistency also reduces the cost of production as cobots waste fewer materials during the manufacturing process.
Most robots used for welding are easy to program. Any experienced welding professional among your employees can program a robot; hence you do not need to hire experts to program a welding robot. Moreover, the end effectors of welding cobots are versatile. They can hold sealants, torches, solder paste, or even glue. Hence you only need to make a single investment to achieve automation for different tasks. Robotic Process Automation (RPA) is put in place to increase efficiency, reduce errors and improve workflow.
However, it is important to note that although robots are capable of MIG, laser, Arc, TIG, plasma, spot, and ultrasonic welding, humans could perform challenging and skill-demanding projects in case of machine malfunction or breakdown. Hence, replacing your skilled welders with welding robots is not prudent.
2. Picking and Packing
Picking and packing are labor-intensive tasks that could be both draining and time-consuming. The disadvantage of using human beings for these tasks is that they cannot work for long periods.
Humans may also make errors that could affect the profits of the business. For instance, if a worker makes a mistake in packaging a product, it could affect the customer’s satisfaction with the product.
Embracing automation prevents the loss of customers due to human error. It enables manufacturers to achieve production goals faster because cobots work longer hours with fewer errors than humans.
3. Palletizing
Palletizing is stacking the packed goods onto pallets for transportation to the market. It is an exhaustive task that could also be potentially dangerous for human workers, particularly those palletizing hazardous or heavy goods. One tiny mistake could lead to a massive loss of stock or fatal injuries that could be prevented with automation.
Adopting the use of robots for palletizing tasks, therefore, reduces the chances of workplace-related injuries and human error. Although small businesses that do not have enough capital or space to set up cobots may not appreciate these advantages, if you own a large plant, automating the palletizing process will mitigate huge risks related to safety or labor shortages.
If you own a business with a mix of low and high production, then quick product changeover is key to the company. You, therefore, need conveyor tracking to synchronize the movement of the packing and palletizing cobot movements with the conveyor. If you produce goods with different shapes, you may also need to purchase a cobot with a vision system.
4. Item Assembly
If you are in the assembly industry, you probably understand how time-consuming and boring assembling tasks can be for human workers. Assembly tasks also require high levels of precision that humans cannot always provide. A small human error in the assembling process could lead to a massive decrease in sales, company brand deterioration, and loss of customers.
You can avoid these risks by automating the assembling process in your company. Cobots will relieve your employees from these time-consuming and labor-intensive tasks while at the same time increasing precision in the assembling process. It will also reduce work safety-related accidents and increase production as the cobots will assemble more parts in a shorter time frame.
5. Material Handling
Material handling involves moving materials around a factory floor or a manufacturing unit. It is a time-consuming task that could cause fatal work-related accidents. Using collaborative robots in material handling could eliminate these safety concerns and hasten production cycles. It could also reduce downtime and the cost of production due to minimized chances of material damage.
6. Quality Inspection
One of the ways of ensuring high customer satisfaction is by producing quality goods. However, workers may not always have the quality you expect because they make mistakes when tired. Due to long working hours, exhausted workers may fail to notice blemishes on products.
Collaborative robots, on the other hand, produce goods with 100% accuracy and can detect even the slightest defects in products. Using cobots in the quality inspection process, therefore, reduces operating costs. Bottom Line The manufacturing industry is becoming competitive by the day.
Hence, it would be best if you started automating your production processes to stay ahead in this competitive market. Although setting up cobots could be a costly endeavor, automation will give you considerable returns on investment in the long term.
Read Also:
Comments Are Closed For This Article