Custom Saw Manufacturing For Your Needs
5 Mins Read
Published on: 22 November 2023
Last Updated on: 24 January 2025
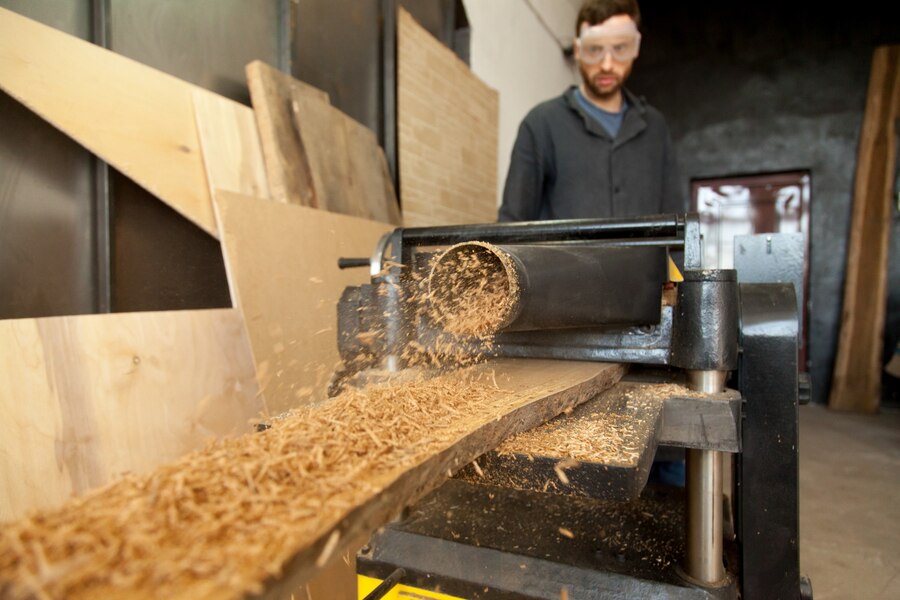
toc impalement
Understanding the ins and outs of saw manufacturing can make a significant difference in your industrial process. Learn about custom sawing, its processes, materials, and investing in your production. Discover how the correct profile can enhance operational efficiency and ensure you have the perfect tools for every need.
Defining Saw Manufacturing
Making saws tailor-made to a customer’s specific needs is called custom saw manufacturing. Unlike generic off-the-shelf products, these saws are meticulously designed and manufactured with particular working conditions or use in mind.
Consequently, these specially engineered saws deliver optimum performance, precise cut quality, enhanced durability, and improved safety features – traits that readily match a client’s particular demand.
A Manufacturing Case Study
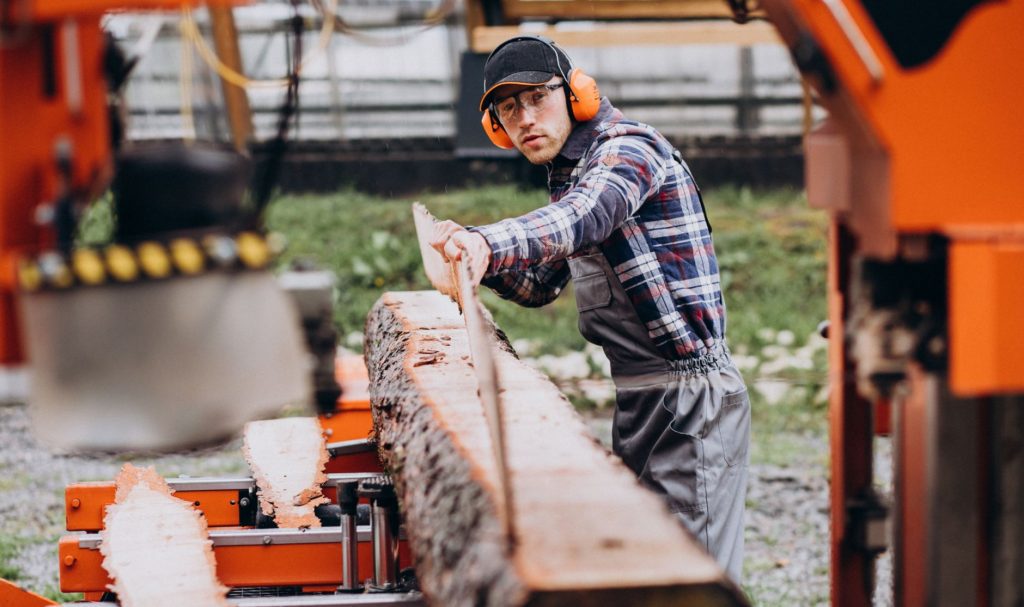
Pacific Trail Manufacturing has been at the forefront of innovative custom saw manufacturing for over 25 years. They have carved a niche by focusing on cutting-edge technology and user-friendly designs that increase productivity while reducing maintenance costs.
Their dedication to high industry standards has made them leaders in producing tailor-made pallet manufacturing equipment and custom cross-cut systems to eliminate common problems experienced in the sawmill industry.
Industrial Sewing Needs
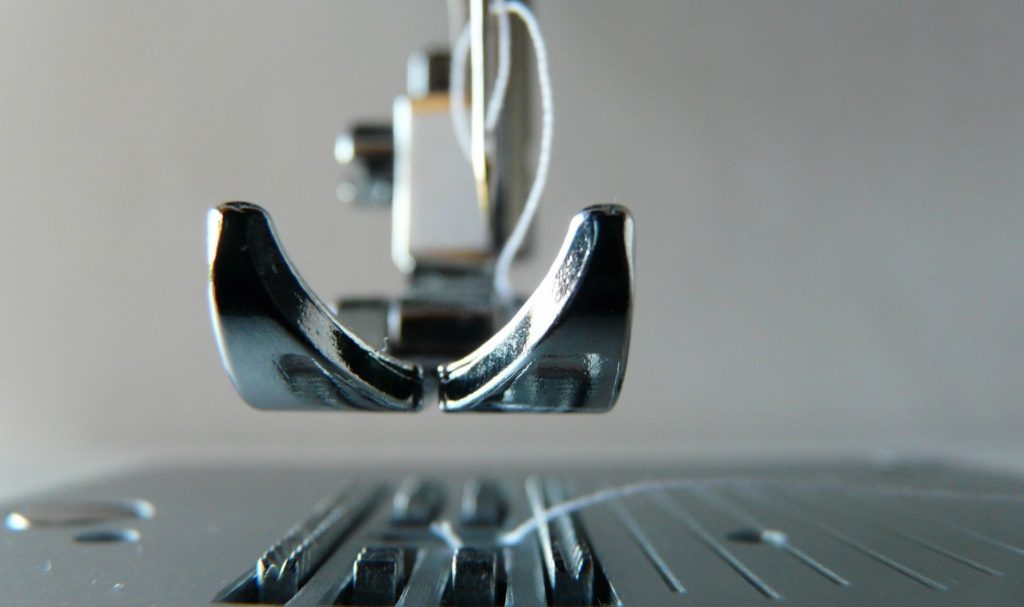
Industrial operations vary significantly, demanding specific tools tailored to their unique challenges. Having the correct saw improves performance efficiency, whether it’s fast-paced mass-production output or detailed precision work.
From food processing industries that require hygienic specialized cutting tools to construction companies needing durable circular saws for heavy-duty operations. A broad range of industrial-grade machinery is necessary to meet different working environments.
Profiling Custom Saws
The profiling process of custom saws starts with the client articulating their cutting needs to the manufacturer. This includes the material to be cut, required frequency and precision, ease of use, maintenance preferences, and available budget.
Using this information, expert engineers devise a prototype saw that is rigorously tested to ensure it meets its performance standards. During this test process, the feedback loop plays a crucial role in achieving the desired end product.
Materials For Saw Manufacturing
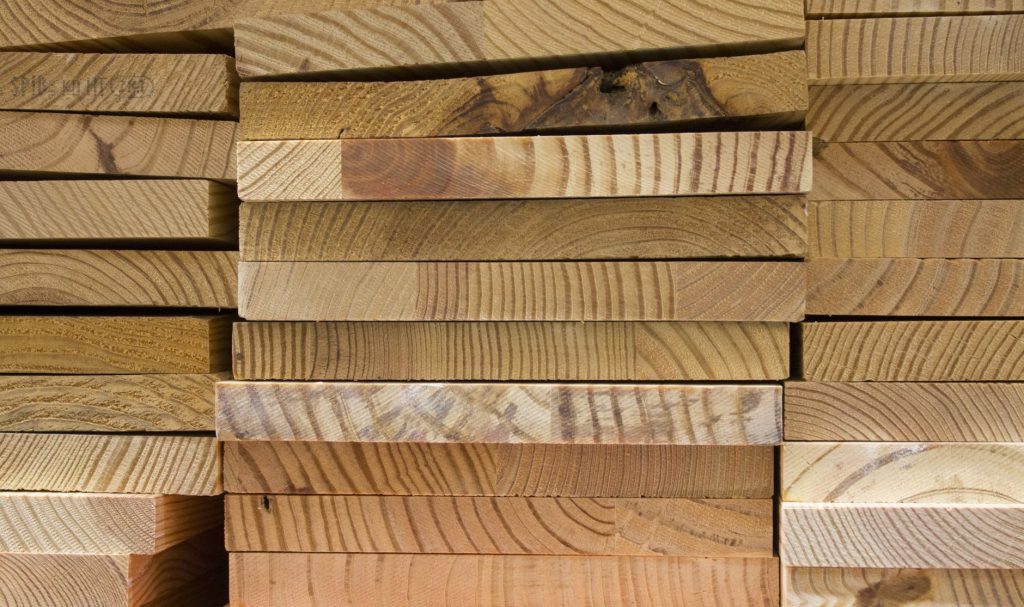
Custom manufacturing uses various materials for different parts of the saw. This means industrial steel might be used for the blade while exotic metals like tungsten carbide are used for the teeth. Each material chosen is not only for sturdiness and durability but also for its capability to maintain sharp edges over time.
Higher-end customizable bandsaws may even incorporate diamond-tipped or cobalt-infused teeth to increase cutting efficiency and tool lifespan. Thus, the choice of material plays an imperative role in the saw’s overall performance and lifespan.
Process Of Custom Sawing
The process begins with understanding your work requirements and designing a custom tool that maximizes efficiency while minimizing potential hazards. Subsequently, your designated profile is accurately cut out from the chosen material using state-of-the-art technology such as CNC machines, plasma cutting, or waterjet techniques.
Ensuring that your sawblade is perfectly balanced and optimized through intelligent design guarantees superior cutting performance and prolongs its operational lifespan by reducing strain on both operator and machine.
Benefit Of Tailor-Made Saws
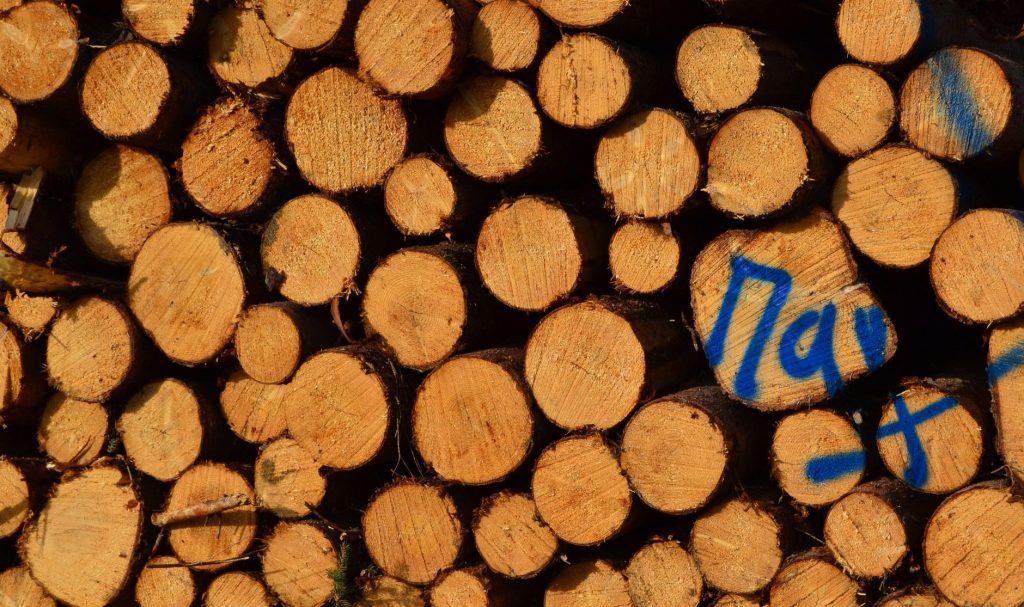
A well-made custom saw can offer numerous benefits over traditional standard products. One significant advantage is increased cut accuracy translating into superior quality output and less waste.
Besides, custom saws can also greatly enhance productivity by allowing quicker and more efficient cuts tailored to specific operational requirements. As a result, you’ll observe an overall production yield and efficiency improvement.
Operating Custom Industrial Saws
Operating custom-designed industrial cutting tools requires technical know-how to leverage their optimal functionality. However, manufacturers nowadays include comprehensive user manuals to assist operators in handling these precision tools safely and effectively.
Moreover, many manufacturers offer training programs to ensure your team can operate the machinery proficiently, underscoring the importance of understanding the intricacies behind safely operating bespoke industrial cutting tools.
Safety Measures In Sawing
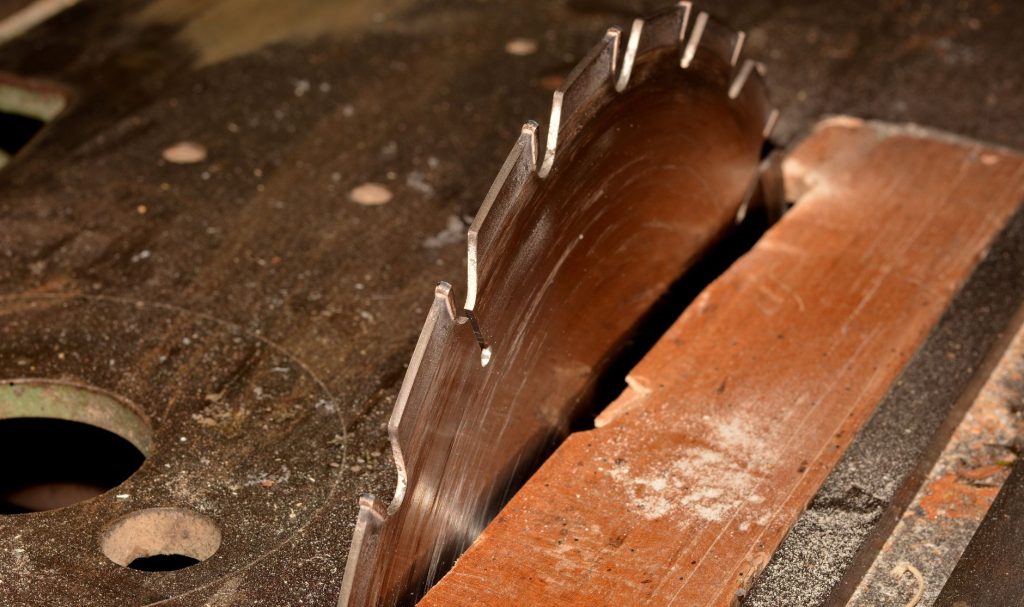
Safety must never take a back seat during operation, regardless of how well a custom saw is designed. Adequate safety measures must be in place to prevent potential accidents.
These could include safety guards to protect operators from flying debris and emergency stop buttons that instantly halt operations. Protective gear for operators, such as gloves, goggles, and respirators, are also essential.
Maintenance Of Custom Saws
Maintenance plays a pivotal role in the performance and longevity of custom saws. Systems should be in place to routinely check the condition of the saw-blades and lubrication levels.
When taken care of properly, products will not just have a longer lifespan – they’ll also deliver reliable performance over time. Many manufacturers give tips on maintenance routines that can help get the most out of their products.
Trends In Saw Manufacturing
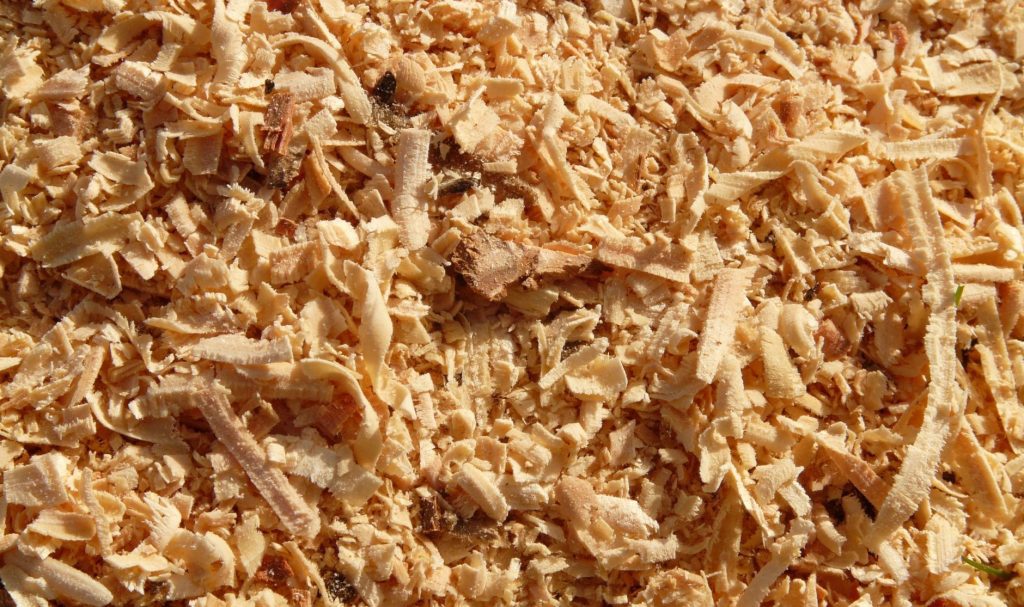
The ever-evolving technology plays a significant role in today’s saw manufacturing. Lights-out manufacturing, where entire operations can run on automation with minimal human involvement, is becoming increasingly popular.
Moreover, advancements like IoT (Internet of Things) are being incorporated to provide real-time data insights about the functioning of the machinery. This helps in preempting any mechanical issues thereby reducing downtime and increasing productivity.
Saw Manufacturing Technologies
Several technologies play distinct roles in saw manufacturing. For instance, robotics is used for precise cutting and assembly. At the same time, artificial intelligence is used to spot defects and control quality during production.
Laser-cutting technology is gaining popularity due to its precision, speed, and versatility. It can cut complex shapes through hard materials while ensuring minimum waste and maximizing accuracy.
Sustainable Practices In Sawing
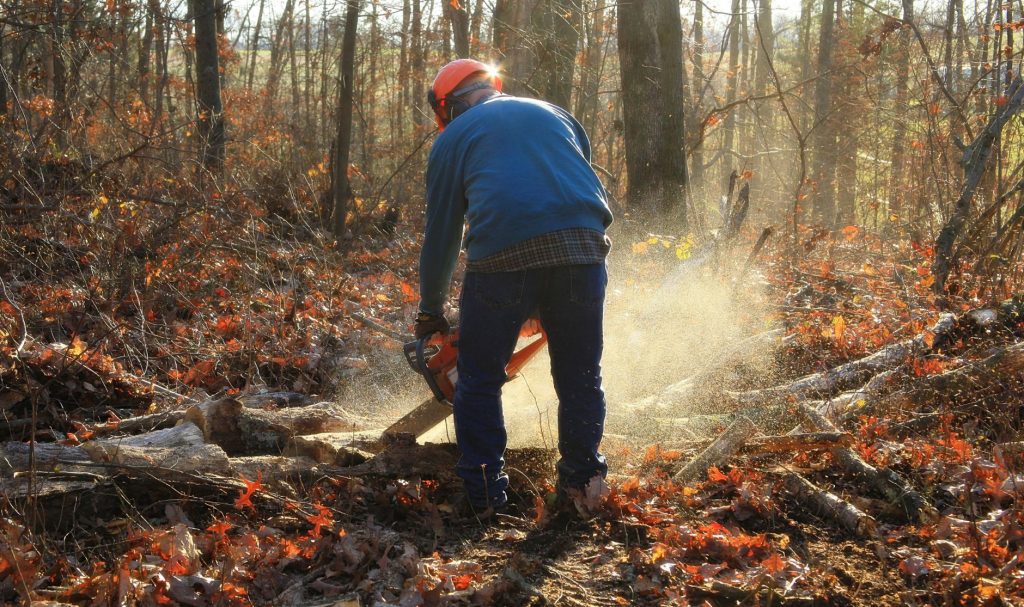
With growing consciousness towards environmental sustainability, manufacturers are turning towards more eco-friendly approaches in sawing. This includes using recyclable materials and reducing wastage during the production process.
Some manufacturers are even exploring energy-efficient machinery that reduces their carbon footprint. It encapsulates the growing need for industries to commit to more sustainable practices.
Quality Control In Manufacturing
Quality control ensures that the custom saws being produced meet the desired standards. Manufacturers use routine inspections, statistical process control, and benchmarking measures to ensure consistent product quality.
The ultimate goal is to provide customers with saws that meet their exact specifications while demonstrating high performance and durability.
Investment In Custom Sawing
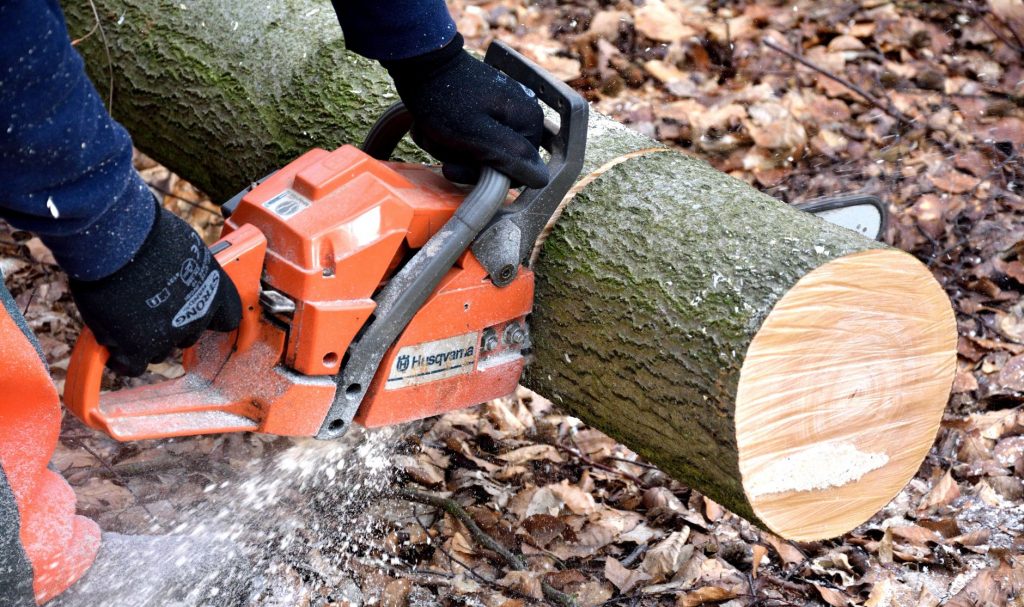
Investing in custom sawing is a strategic move for businesses striving for efficiency. While it might entail higher upfront costs, it can significantly reduce operational costs over time by increasing productivity and reducing waste.
Moreover, it allows companies to operate on their terms rather than adapting their work processes according to available tools.
Skills For Saw Operators
Beyond the physical strength needed to handle heavy machinery, custom saw operators must possess various skills. This includes technical know-how about the operation and maintenance of these machines, as well as critical thinking to troubleshoot potential problems.
Saw operators generally undergo hands-on training where they learn about safety regulations, machine setup, and blueprint reading, among others. Interpersonal skills are also crucial as operators often work very closely with teams.
To Conclude
Custom saw manufacturing presents a realm of possibilities to industries – enhancing operational efficiency, ensuring safety and allowing room for specific adjustments. The investment is worth it for businesses aiming to streamline their processes and achieve output that matches their unique needs. Expanding technologies boosts this promise further, as you progress towards more automated, sustainable ways of producing tailor-made saws.
Read Also:
Comments Are Closed For This Article