Reducing Downtime & Boosting Efficiency: A Case Study on Predictive Maintenance Solutions
21 February 2025
5 Mins Read
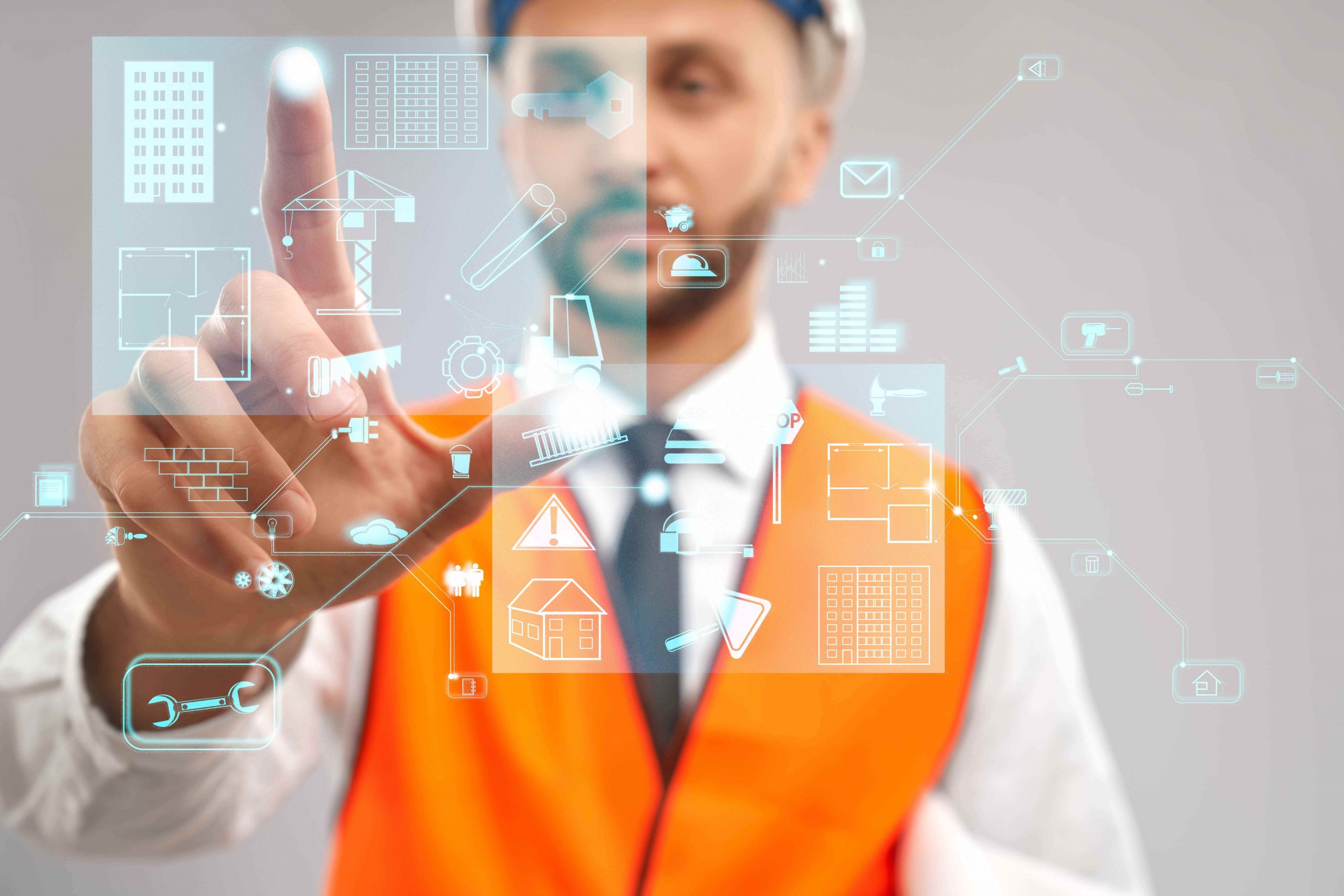
toc impalement
The highly competitive business landscape in 2025 suggests that entrepreneurs must take prominent operational approaches without errors. Therefore, reducing downtime and boosting operational efficiency should be the first priority of modern business enthusiasts.
The average cost of downtime across industries was about $5600/minute. However, this will be more critical with the latest data on downtime costs.
According to recent research, the downtime cost has grown to $9,000/minute, increasing the risk factors for various industries. While 98% of organizations are facing huge downtime losses, even if it happens for an hour, predictive maintenance solutions are becoming a more prominent solution across industries.
To prevent costly disruptions, you are required to make smart moves, and Cloud-based predictive maintenance platforms can give you that chance. From transportation to healthcare, the implementation of predictive maintenance solutions is the most impactful way to reduce downtime and increase productivity with efficiency in your organization.
But what is predictive maintenance?
Let’s explore here!
What is Predictive Maintenance?
Predictive maintenance solutions involve the direct involvement of IoT sensors, data science, and artificial intelligence (AI). Asset maintenance is a common area of concern for most businesses. Whether it is a part of an automobile or a solar panel, the chances of sudden breakdown are very low with these assets.
However, once you experience a breakdown, it will take time to resolve the issues and get back to work. Though in most cases, multiple warnings or singles will be present, initial warning signs are mostly overlooked by human operators or administrators.
Well, this is not their fault, as warning signs are not always correct, and people try to trust their experience over machinery.
This is where predictive maintenance solutions come along the way to benefit an organization with fast-paced technological monitoring.
What does it include?
- A real-time data collection
- Data processing through machine learning (ML)
- Collaborating with administrators with proper warnings and predictive alerts.
This way, the administrator can focus on early maintenance to avoid any breakdown and repair machinery even before any hazard occurs. Well, this is very advanced and unlikely to be the case with traditional approaches like preventive maintenance (scheduled maintenance regardless of equipment condition) and reactive maintenance (repairing after failure).
This way, you can not only reduce downtime and increase the operational efficiency of your products but also avoid unnecessary repairs and extend asset life.
Case Study: Predictive Maintenance in Manufacturing
Let’s take a look at a real-world example of predictive maintenance for automotive industry.
Try to understand how industrial automation and predictive analytics bring justice to the overall manufacturing and delivery of a business.
Background
General Electric (GE) has revolutionized its maintenance process to improve its operational efficiency while saving costs and time. However, they had a challenge in the past.
Challenge
This American multinational conglomerate, once based on a traditional maintenance process, faced a lot of challenges. Manufacturing equipment failure leads to delivery delays and costly downtime. This also includes the increased operational cost of heavy repair and the slow working process with more resources.
GE faced a challenge in predicting failures in their heavy equipment with reactive and preventive maintenance processes.
Therefore, the new challenge for them was to find a reliable and advanced management solution for manufacturing equipment.
Solution
The company decided to implement a predictive maintenance solution!
AI-powered predictive maintenance system helped GE utilize machine learning algorithms to monitor and analyze real-time data on their equipment. This way, they were able to collect sensors’ embedded data from their equipment.
On the other hand, they already had the operational data in hand. After that, they were able to integrate both data and, with the help of AI analytics, make a meaningful prediction.
The AI systems can detect unusual patterns quite effectively to understand potential future options.
Results
The implementation of predictive maintenance solutions in GE helped them a lot in various ways. Some of the notable benefits are-
- Reduced Downtime: With predictive maintenance, GE was able to drastically reduce the chances of unexpected equipment failure. Therefore, they are now at the top of their operational efficiency.
- Cost Savings: When you address issues even before it happens, you do not need to pay for the heavy maintenance. GE saved massively on their repair costs while also extending the lifespan of equipment with advanced maintenance.
- Optimized Maintenance Schedule: While focusing on more important tasks, GE was able to control optimized schedule maintenance with the help of AI predictions.
Best Practices for Implementing Predictive Maintenance
To replicate the success of GE’s case study in your own organization, it’s important to follow best practices when implementing predictive maintenance. Here are some key considerations-
1. Start Small and Scale Up
Begin by focusing on the most critical assets with the highest failure risk. This will help demonstrate the value of predictive maintenance early on. Once proven, you can gradually expand the solution to cover more equipment across your operations.
2. Invest in Quality Sensors and IoT Devices
Reliable data collection is the foundation of predictive maintenance. Invest in high-quality sensors and IoT devices to ensure accurate and real-time data from your machines. Poor data quality will compromise the accuracy of predictions.
3. Choose the Right Software and Analytics Tools
The software you choose should be able to handle large volumes of data and apply sophisticated analytics like machine learning to make accurate predictions. Opt for solutions that are scalable, easy to integrate with existing systems, and offer real-time insights.
4. Train Your Team
Predictive maintenance requires a shift in the way your team approaches maintenance. Ensure that technicians and engineers are trained on how to interpret the data and act on insights provided by the system. Their expertise is essential to making effective decisions.
5. Continuously Monitor and Improve
As with any technology-driven initiative, predictive maintenance systems need to be continually monitored and refined. Regularly assess performance, fine-tune machine learning algorithms, and ensure that your system adapts to changing conditions and new data sources.
Invest in a Long-Term Maintenace Solution
Predictive maintenance solutions revolutionized the way industries approach asset management and maintenance. If you stay back from collecting real-time data and maintaining your equipment based on advanced predictions, you might fall back into the competition.
However, investing in predictive maintenance solutions might seem a significant upfront investment, but it comes with long-term benefits. You can take it as a strategic move to avoid all future maintenance failures.
READ MORE:
Comments Are Closed For This Article