6 Reasons to Reduce Unplanned Downtime in Manufacturing
5 Mins Read
Published on: 13 May 2023
Last Updated on: 21 November 2024
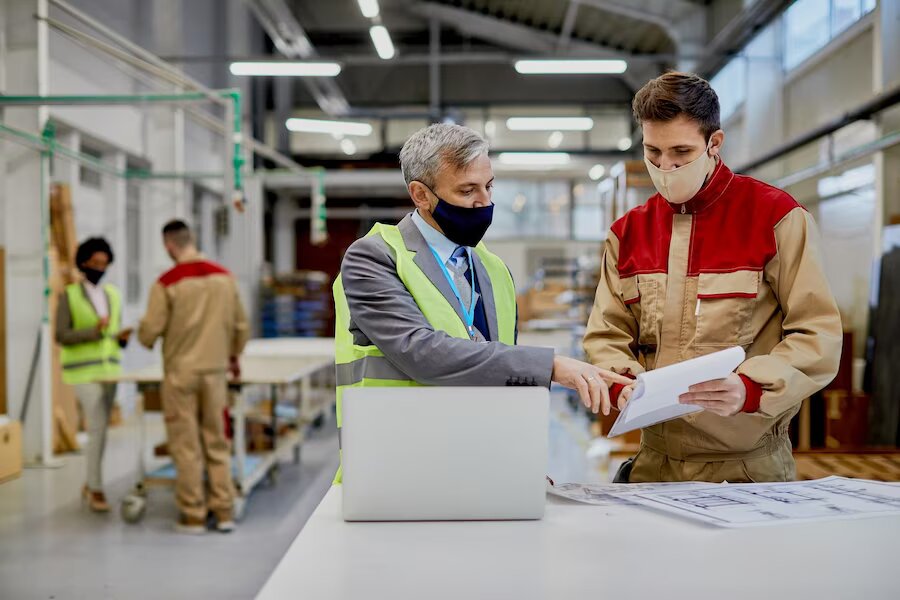
toc impalement
For any manufacturing plant, unplanned downtime is an avoidable issue that can come at a high cost from both a financial and operational perspective. Poorly functioning machinery, out-of-control production processes, and unreliable equipment are all contributing factors to unplanned downtime in the manufacturing industry.
The trend of unplanned downtime continues to increase. As a result, manufacturers need to take action to protect their investments. Reducing unplanned downtime has numerous benefits for any type of manufacturing business. Hence, it’s worth considering taking steps to mitigate this risk.
This article will explore six genuine reasons why reducing unplanned downtime should be a priority for your business. From improving overall efficiency to increasing customer satisfaction rates, addressing unplanned downtime is essential for manufacturing success. The importance is simply growing in an increasingly competitive world.
What Do We Mean By Downtime In Manufacturing?
Downtime can range from something as small as a few minutes of downtime needed to inspect a moving part to shutting down production lines for days in order to repair and modernize them properly.
Both types of downtime cost businesses millions every year in lost productivity and revenue, so it’s essential for manufacturers around the world to find ways to minimize this period of disruption and keep their operations running smoothly.
6 Reasons to Reduce Unplanned Downtime in Manufacturing
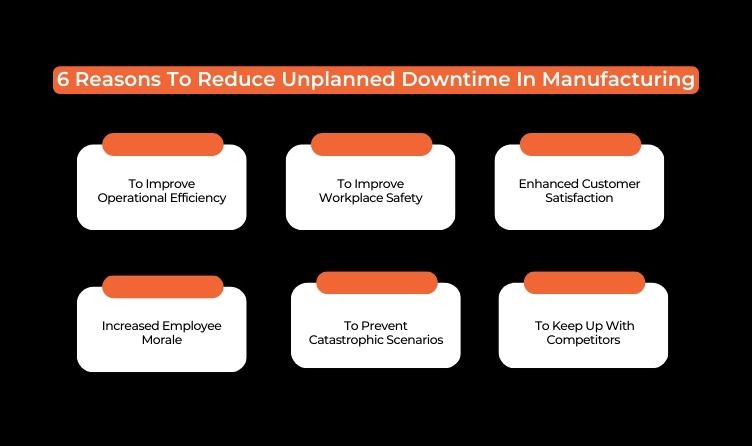
Several strategies have proven effective. Such as dedicated storage space for spare parts, scheduling maintenance according to historical patterns, and so much more.
Here are some of the reasons why you need to improve and reduce downtime. Therefore, let us dive right in!
1. To Improve Operational Efficiency
For manufacturing businesses, operational efficiency is essential not only for meeting financial goals but also for ensuring customer satisfaction. However, one real threat to achieving operational efficiency is unplanned downtime. It disrupts the flow of efficiency in manufacturing operations.
Achieving operational efficiency requires a commitment to eliminate unplanned downtime, which interrupts the production process and can lead to lost profits, reduced customer service quality, and even safety risks.
This means investing in processes and systems that enable quick response times when equipment problems occur, along with regularly scheduled maintenance.
Improved communication between various departments during the production process is critical as well, as it helps identify and address weaknesses in areas related to unplanned downtime, such as machine or spoke shortages.
2. To Improve Workplace Safety
Safety should always be a top priority in the workplace and, especially in manufacturing. Unplanned downtime can cause significant inconveniences and put employees at risk of harm.
This also makes it a significant reason for reducing unplanned downtime in manufacturing industries. To reduce unplanned downtime in manufacturing, implementing better safety measures is a must. This could include providing regular staff training with specific instructions on how to operate machinery or equipment properly.
Also, installing protective guards, machine downtime tracking tools, and other warning devices around potential hazards can help prevent employee injuries and possible accidents, while proper PPE can prevent dust and other hazardous exposures.
Companies also need to ensure that their machines are regularly serviced and inspected by qualified personnel. This is to catch any potential problems before they become huge in the long run. When it comes down to it, workplace safety should be more than just a requirement – it should be something that all businesses prioritize in order to keep employees safe from harm.
3. Enhanced Customer Satisfaction
One of the things that please the customers is to always meet their needs, even before the set time frame. It enhanced customer satisfaction, which is of the utmost importance in any manufacturing business. Customer satisfaction is directly related to company success.
When a business proactively reduces possible sources of unplanned downtimes, such as equipment malfunctions or supply chain disruptions, it makes sure that the production process never stands still, enabling the company to exceed customer expectations with its products or services consistently.
An operational uptime that meets even the most demanding requirements results in increased customer trust and loyalty, which translates into repeat purchases from satisfied customers.
4. Increased Employee Morale
Reducing unplanned downtime in manufacturing can significantly increase employee morale. It also helps to create an environment where workers feel safe, secure, and respected. When employees feel that the company values their work, they can be more engaged in their tasks. Subsequently, feel a greater sense of satisfaction from the job.
When manufacturing operations are run smoothly and efficiently, with minimal downtime, it creates a sense of accomplishment among the staff. This can then lead to higher morale, which can translate into improved employee retention and loyalty rates. As a result, ensuring the company continues to benefit from its most valuable asset.
5. To Prevent Catastrophic Scenarios
A lot of catastrophic scenarios can arise as a result of unplanned downtime in a manufacturing plant. Aberrations include fire and explosion risks, toxic gas emissions, and other environmental hazards.
These unsuitable incidents can cost a business thousands, if not millions, of dollars in damages, legal fees, and fines. However, these problems can be easily avoided with careful planning and execution.
6. To Keep Up With Competitors
Obviously, the role competitors play in the industry must be noticed. For example, most manufacturing businesses now provide both goods and services that are of high quality and reasonably priced as a result of competition among manufacturing companies.
As such, it is essential to maintain an up-to-date production process to keep up with the competition. The updated production process can also help you avoid being relegated to the bottom of the table.
One of the ways to ensure that is to reduce unplanned downtime in the manufacturing plant. This way, the manufacturer will have a better chance of competing with other manufacturing businesses on all fronts. This includes pricing, product range, etc.
Bottomline
Reducing unplanned downtime in manufacturing is a must for any business looking to succeed. Not only does it improve operational efficiency and customer satisfaction rates, but it also helps keep employees safe. Subsequently, it also prevents catastrophic scenarios and allows businesses to stay competitive.
You can help significantly minimize the risks of unplanned downtime by investing in quick response arrays and scheduled maintenance. Both of them allow businesses the space to rectify and move ahead.
Taking steps now to mitigate this risk will ensure your business remains successful in the future.
Read Also:
Comments Are Closed For This Article