Risk Management in Logistics: Mitigating Challenges for US Shipping Companies
17 Mins Read
Published on: 28 March 2024
Last Updated on: 17 July 2024
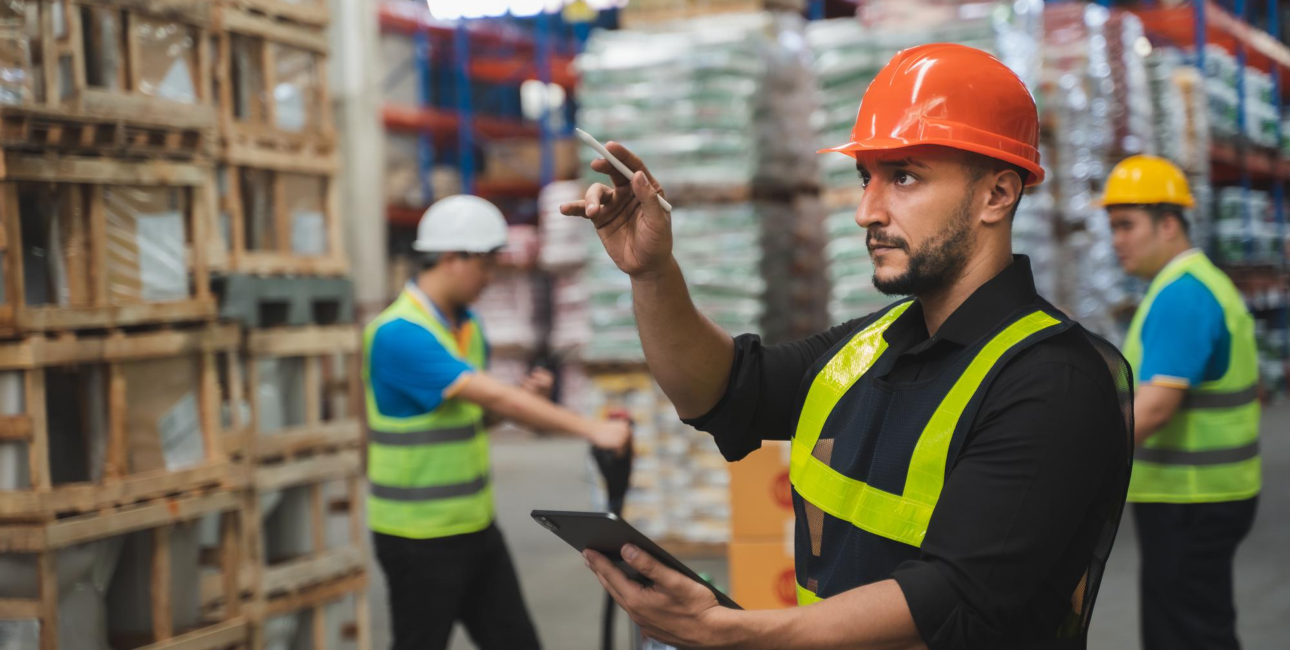
toc impalement
The supply chain and logistics department keep the business world moving and operational. However, accidents and risky situations may disrupt the workflow because the entire process runs through different phases. That’s where a risk management strategy becomes elemental.
Multiple incidents of IT system failure, labor disputes, machinery breakdown, and injuries hamper operations and decrease profitability. Such risks are often specific and come under certain groups of risks.
But, as dangerous as they might be, they are not something a business cannot handle. That’s where supply chain and logistics risk management strategies come in. It starts with the risks and possible measures one can identify to solve them. Followed by that are safety protocols, training programs, and monitoring options.
Here is a LONG study that sheds some light on risk management in logistics and supply chain management.
What Does Risk Management Mean in Logistics and Supply Chains?
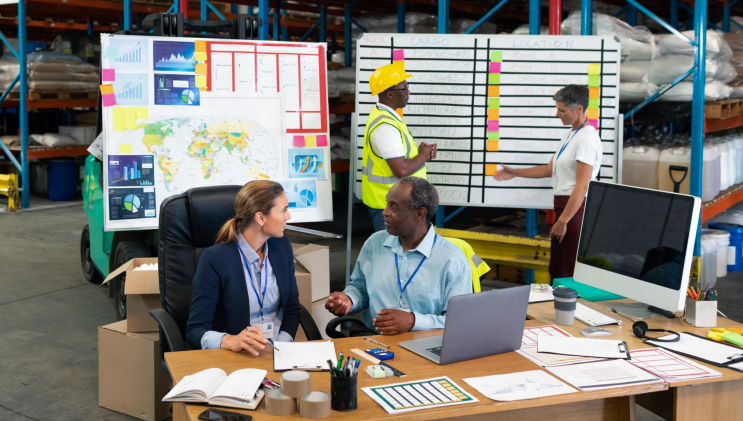
Risk management in supply chain and logistics is a deliberate tactic to identify, prevent, solve, and mitigate risks. This is a multiphase approach ensuring safety and operational efficiency in the logistics industry.
The logistics industry works in multiple phases. It starts with production and storage, which is also called inbound logistics. The delivery of the finished products comes under outbound logistics. The industry can develop risk at any of those phases in the logistics chain.
Through proper risk management tactics in the logistics department, it is possible to fortify a business. Strategists and planners can help build preventive measures and backup plans to keep the supply chain business operational.
Logistics and supply chain risk management require close monitoring every step of the way. This is why the enterprise resource planning of a company has to have a comprehensive oversight of the supply chain management spectrum.
Core Operational Risk in Logistics System
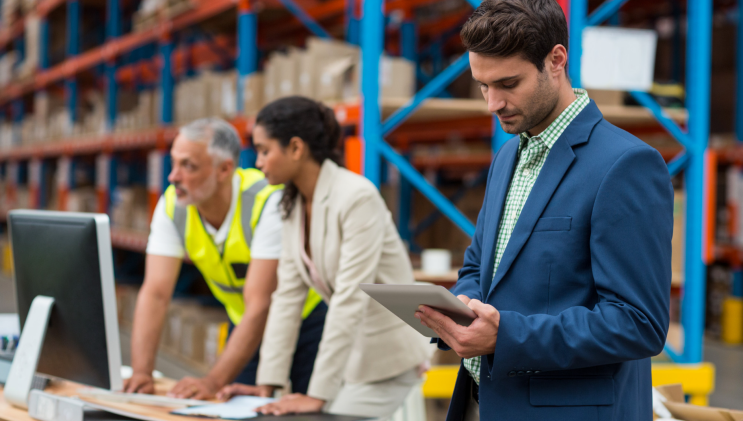
Since the logistics industry operates in multiple layers, it is potentially prone to different types of operational risks. Here are some examples of the same –
Demand risk
A miscalculation in product demands can cause demand risks in logistics. A lack of understanding of the annual purchasing trends usually causes this risk. Furthermore, an unpredictable demand in the market can also cause demand risk.
Unresponsive supply chain
A supply chain fails to reach a stable point when the market demand is unpredictable, and the business environment is unstable. In addition, fluctuating customer demands, unanticipated actions by competitors, and market dynamics keep the supply chain staggering through difficulty.
Disruption in transportation
Transportation disruption can cause late deliveries and leave the customers unsatisfied. Furthermore, it can also incur additional spending on the business’s part.
Damages to Products
Goods and products might get damaged during any of the phases of the logistics and supply chain’s operation. While in transit, or during packaging, or inefficient handling can cause the products to get damaged.
Cargo Theft
Cargo theft has been one of the major problems in the supply chain. A July CargoNet study reveals that
“cargo theft incidents increased 57% year-over-year, accounting for $44 million in stolen shipments in the second quarter of 2023.”
Big companies secure cargo freight by taking measures such as using shipping container seals, GPS container tracking, or by using smart containers. Some cargo theft prevention methods would be –
- Tag cargo with trackable active tags.
- Setting up a real-time supply chain monitoring system also helps.
- Acting upon potential supply chain thefts as certain trackers set off the alert.
Failures in Communication
Parties involved in the supply chain and logistics often have miscommunication issues and failures in understanding the procedure. This results in delays in operations and breaks down the logistics chain.
Operational risks in the logistics and supply chain do not only mean the business’s failure. It can also cause occupational risks for employees.
Businesses are always on the lookout to properly deliver products promptly, safely, and without facing lots of risks. However, the specifics of operational risk management in logistics are not clear to many businesses.
There is a possibility for businesses to assume that the logistic risk management strategies are superfluous. Also, some businesses can rest assured, assuming their supplier’s service providers already have plans in place. However, it is not necessary for the supplier’s contingency to align with the logistics business. That is why building a strategic supply chain management process is integral.
Most companies use the following to create their supply chain management strategy –
- Spreadsheets
- LSCM software
No matter how intricate supply chain management and the process is, it is important.
Why is Risk Management in Logistics and Supply Chains Important?
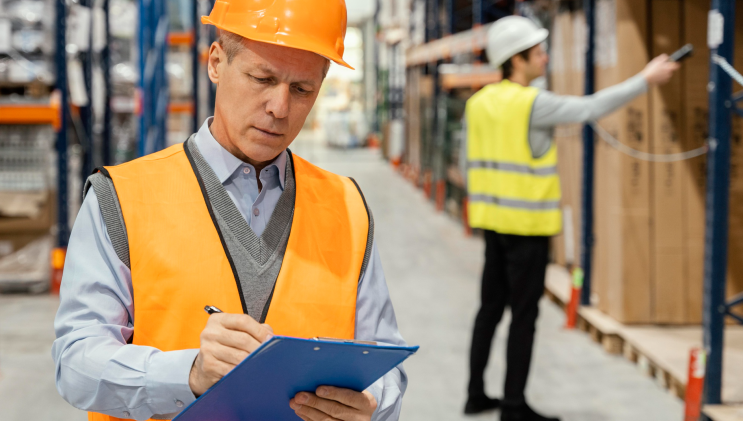
- The supply chain of a business is what keeps a business operational. A minor fault in the operation can throw the entire business out of balance.
- It keeps the internal business operations integrated with the external affairs of the business, resulting in smooth profitability.
- Proper supply and chain risk management processes help reduce unwanted financial downfall.
- An LRM process gives businesses an eagle’s eye view over the entire logistics and supply chain.
- Maintaining a well-managed logistics and supply chain is important to any business. A risk management strategy ensures that.
Different Types of Risks in Logistics and Supply Chain Management
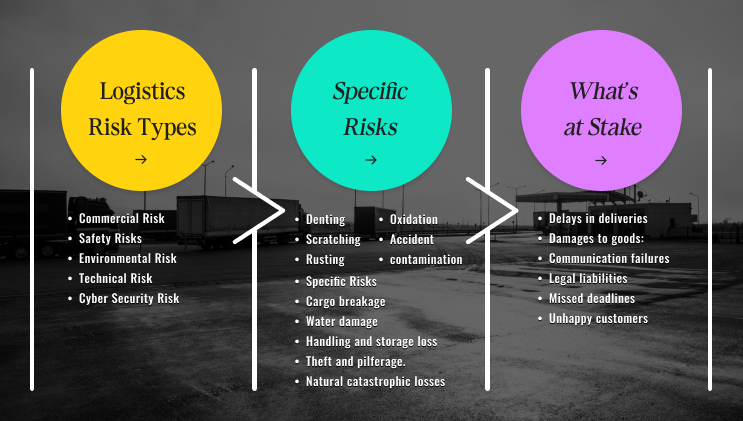
There is no specific definition of risk in the logistics and supply chain management industry. However, any minor to major disruptions can cause risk to the entire supply chain and logistics. Such disruptions can affect production, revenue, processes, delivery, and customer services.
That’s why supply chain leaders take responsibility for assessing the risks and managing them accordingly based on various metrics. Most risks in logistics and supply chain management are related to geopolitical, economic, and environmental phenomena. Logistics and supply chain businesses usually face some of the following risks –
Labor & Union Issues
The manufacturing sphere, or the primary phase of the logistics industry, faces labor and union-related issues. Often, altering the employee contracts, settling wages for workers, and implementing specific work hours result in feuds and extend the entire process of the supply chain. Businesses need to maintain accurate insurance policies to ensure minimal levels of disruptions in the supply chain and logistics.
Financial risks
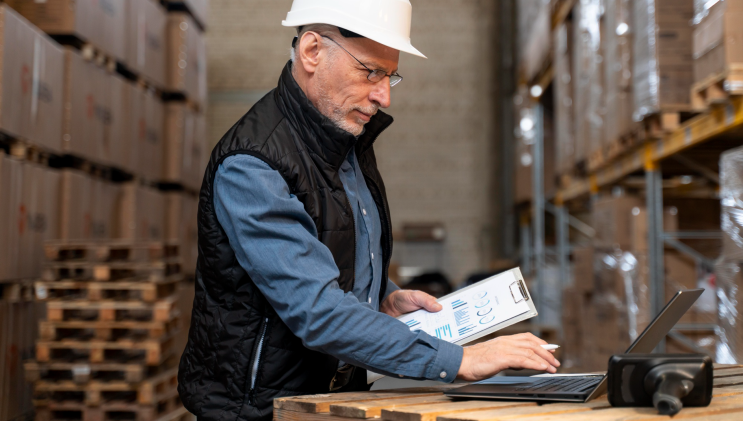
Unfavorable or unexpected shifts can affect logistics and supply chain businesses. These risks can affect the suppliers. It can cause logistics complications and unpredictable cost overruns. Further financial risks arise from budget overruns, increased funding requirements, and changes in the project’s scope. Logistics often miss project milestones due to financial risks.
Supply Risks
Inconsistent delivery of raw materials results in supply risk in logistics. Delivery of products and raw materials should be timely, or damage to raw materials results in supply risk in logistics.
Demand risks
Inaccurate product demand forecasting can result in logistics sector demand risks. It usually gets affected by inadequate visions of the annual trends of purchasing. However, if the market keeps fluctuating, it results in demand risks.
Business Risks
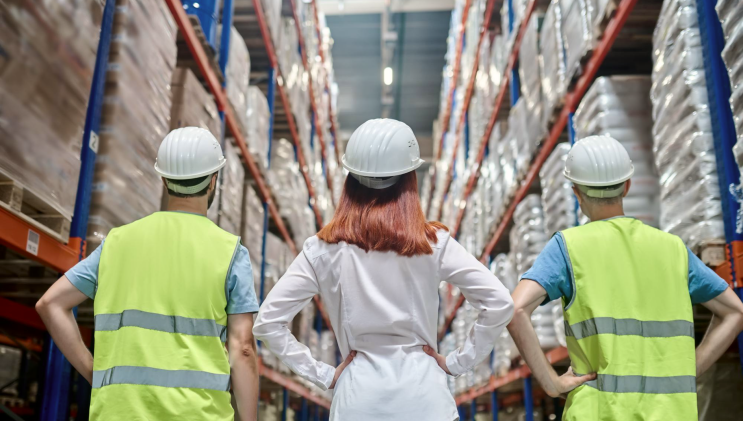
Certain entities within a business are vital to its operations. However, unexpected changes and shifts internally can bring business risks within the logistics and supply chain sector.
Environmental Risks
Some risks within the supply chain industry are not avoidable. These are the environmental risks or calamities that affect and disrupt the logistics and supply chain operations. Some common examples would be floods, pandemics, earthquakes, or other natural disasters of different degrees.
Although natural calamities or environmental risks are unforeseeable, a few instances still prove the indomitable growth of the logistics department. The 2020 pandemic had an immense effect on the supply chain and logistics. Despite that, it projects a CAGR of 11.2% from 2020 to 2027. In 2020, the market had an estimated $37.41 billion.
Geopolitical Risks
Geopolitical issues have effects on businesses and supply chain operations. Such issues or risks are related to political instability, civil unrest, or corruption. These issues affect the country’s tourism, businesses, and logistical operations. Usually, minor issues are dealt with using certain risk management tactics. However, when multiple geopolitical issues coexist, it results in a difficult situation for the supply chain.
Cybersecurity Risks
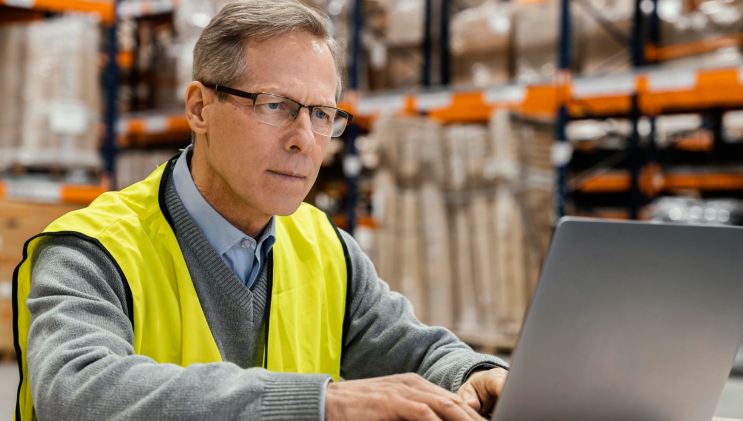
Cybersecurity or intellectual property theft-related issues can also affect the supply chain. Many businesses have faced instances of their trade secrets being leaked or critical business information stolen. Some common incidents related to cybersecurity issues include ransomware attacks, theft of intellectual property, or data breaches.
Economic Risks
Economic risks can emerge in the supply chain industry because of demand fluctuations, delays in the port and borders, or fluctuations in the currency rate. The scarcity of raw materials and price volatility can result in economic risks for the logistics and supply chain industry.
Create a Risk Management Process for Logistics
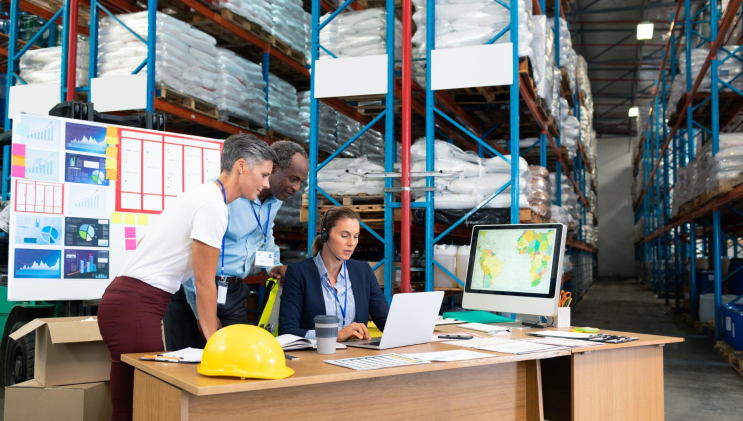
Most logistics and supply chain companies usually follow the risk management process as stated below –
Spotting Risks in the Supply Chain
The first step toward creating an effective logistic risk management strategy requires proper identification of potential risks. A proper understanding of potential risks allows businesses to build preventive plans of action to use them when the need arises.
However, business owners should remember to not only consider the operational risks. External factors like geopolitical issues, demand risks, or environmental risks are also there.
A good way to start would be by looking inside the supply chain first and considering the critical operations.
The critical operations may include services, staff, and suppliers. The next step would be noting down the things that can affect the workflow of all these crucial elements within the supply chain. Some common incidents that potentially affect the key elements of the supply chain are –
- Workers’ strike.
- Truck accident.
- Poor quality logistic provider.
Risk Analysis of Potential Risks
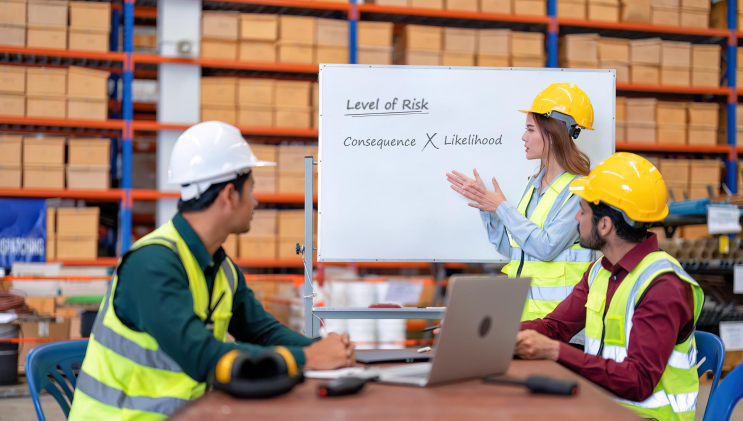
Risk analysis is the second step in the logistics risk management strategy. It is important to understand the impact of any potential risk identified. The degree of impact any potential risks pose helps business owners prioritize actions helping in damage control.
It allows for the anticipated amount of damage the business might face because of certain risks. Also, with the business’ risk appetite in place, alongside risk analysis data, logistics risk managers can take immediate actions for major risks.
Here is a common way of evaluating the risk levels –
level of risk = consequence x likelihood
Usually, the likelihood of a risk is related to the probability of its occurrence within certain time frame. The consequence part is the assumed level of financial loss the business can face due to a single occurrence of this risk.
Treating Risks
A logistic risk management strategy should not only involve identification or risk and its analysis. It is critical to develop actionable steps to be taken during certain occurrences. These steps and actions need to be risk-specific, with different plans of action for each of them.
When developing a plan of action, remember to enlist the following factors:
- Risk treatment process.
- People are accountable for certain actions.
- Investment involved.
- Potential benefits and outcomes of the treatment.
- Chances of success.
- Strategies in place to evaluate the treatment success.
Keep Updating the Risk Management Process
The risk management strategy for an ever-changing landscape like a supply chain also needs to be ever-changing. There should be measurable KPIs to evaluate the strategy’s performance and success. If the strategy is not performing as per expectation, it needs to be changed.
Since the industry itself is evolving, a plan that worked before might become obsolete in the near future. So, there should be a schedule to revisit and review the plan of action or risk treatment procedures. It needs to be modified and updated according to the current industry scenario and risk analysis of current potential risks.
10 Logistics & Supply Chain Risk Management Strategies To Follow
A strong process is the foundation of risk management strategies. Once the process is ready, strategies can be implemented as the need for it arises. Here are ten popular logistics risk management strategies.
1. The PPPR Risk Management Model
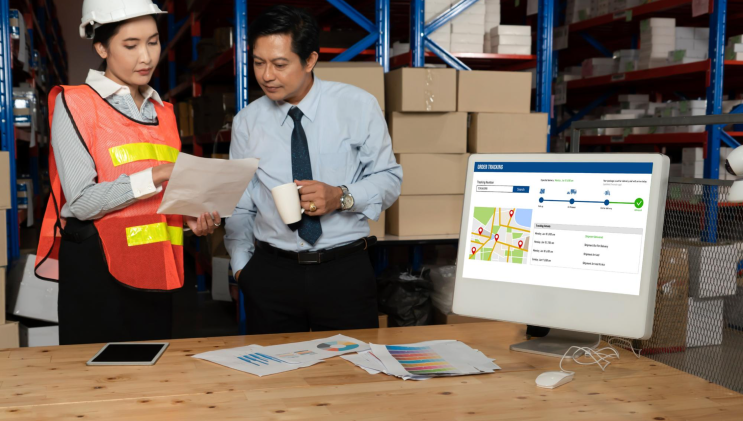
Before trying an innovative method, working with what already works is best. The PPPR method is a widely used and relied-upon process for logistic risk management. PPPR risk management strategy consists of four steps –
Prevention: This step involves taking precautionary measures to mitigate the risk level.
Preparedness: this step is all about developing a contingency plan to avoid or face certain emergencies.
Response: this phase involves executing the contingency plan to help withstand the effects of the disruptive event.
Recovery: The recovery phase of the PPPR management model deals with resuming operations and running them more smoothly than ever.
2. Managing Environmental Risks in Logistics
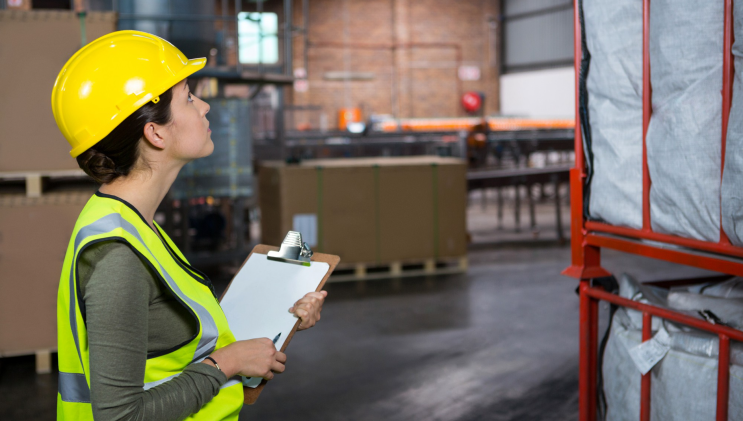
Environmental risks in logistics and supply chain management are a big issue and one that needs to be handled properly. There is no possible way of preventing environmental risks. But some damage control measures can be taken. Through clean and clear visibility of the supply chain structure, it is possible to come up with better risk management steps.
Strengthening the weak areas of the supply chain and building contingency plans are elements of environmental risk management in the supply chain. Here are some common strategies to follow to mitigate such risks –
Multisource the Suppliers
Diversify your suppliers like you would diversify your stock portfolio. It helps to categorize the suppliers based on their prices. However, it is critical to assess the possible impact if there is any disruption. Suppliers that produce from different locations are less risk-prone compared to suppliers that produce from one location.
To reduce the time cycle of product development and delivery, opt for suppliers that operate close to your base of operation. Yes, regional suppliers are a little on the expensive side. However, reduced delivery time can help mitigate potential risks.
Stress Test
Having an outline of the supply chain is good. But comprehensive stress tests on a frequent basis should reveal vulnerabilities hidden inside the chain.
Build Buffer for Inventory
Building buffers for inventory and capacity can help fight natural calamities. However, when it comes to creating buffer capacity, expansion into new areas and the launch of new products are the best times for that. To reduce environmental risks, stockpile products during high-risk periods.
Use Efficient Product Solutions
When using risk management software for supply chain management, it is best to use cloud-based software and the same data architecture used throughout the network. Such product solutions and software should help keep the entire chain operational.
Additionally, the following risk management tactics can also keep the entire environment and risk management process operational –
- Allocating leadership responsibilities.
- Corporate governance integrated with environmental risk management.
- Building an environmental risk register.
- Preparing an environmental compliance register.
- Assessing environmental aspects and impacts.
- Understanding the risk context.
3. Cyber Security Risk management
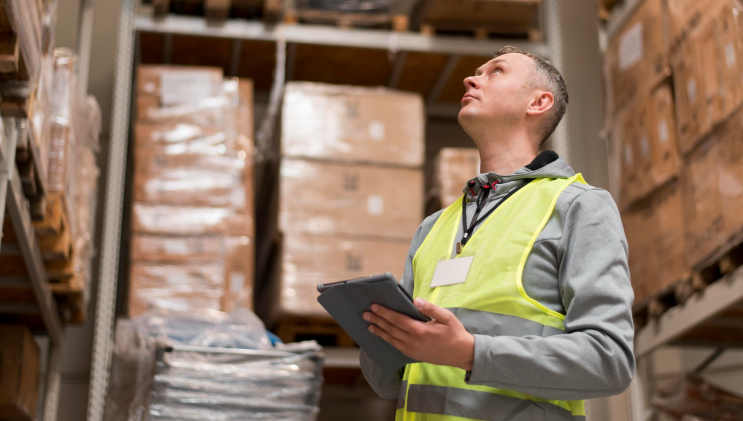
Many businesses tend to use technologies like IoT to improve the operations of their logistics and supply chains. However, such uses also come with the risk of being exposed to different cybersecurity threats. Malware, ransomware, hacking, and phishing are some common cyber security threats that can affect a supply chain and logistics network. On top of environmental risks, this risk can take a terrific shape.
Following are some steps to help manage and mitigate these risks –
- A built-in compliance standard should be there for all the suppliers, vendors, and manufacturers to stay compliant. It should help create the first line of defense.
- Next, there should be a quality security control system. The access should be available to people on the basis of their level of clearance.
- Before signing any contracts, performing an in-depth vendor risk assessment is crucial.
- Implementation of data stewardship should help understand who has access to which data and their responsibilities to those data.
- Make cybersecurity compliance training mandatory for all employees.
- Use and implement software for all-around visibility over the entire supply chain. This should help with the quick identification of problems.
- Work with the vendors in the supply chain network to develop a unified plan for business recovery to help continue the business.
- Build a data backup control to store and safeguard useful data backups.
- Build a rule for regularly updating company software related to spyware, anti-virus, and firewall software solutions. Advanced cyber security control protocols such as DNS filtering network access control also need to be looked at.
4. Improve Supply Chain Visibility
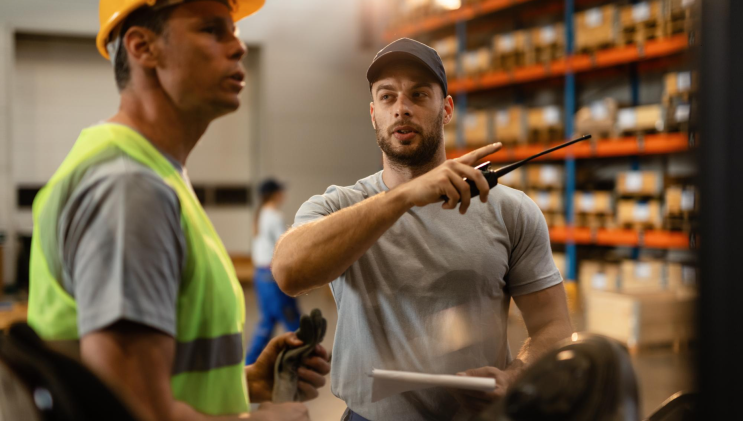
Better visibility over the entire supply chain can help businesses gain valuable insights. These insights help prevent problems before they arise. A good understanding of financial stability can help select partners. Different credit rating agencies are helpful in this respect.
These ratings help businesses tackle problems related to dealing with third-party vendors. The downside of this is its limitation in dealing with existing suppliers and vendors. However, businesses will certainly benefit from building meaningful relationships with suppliers and vendors. Some solutions in this case would be –
- Finding out software solutions that provide an overarching insight into the supply chain. With features like updated delivery time and tracking options, it would be easier to live up to the customers’ expectations.
- Automated reports, IoT sensors in the containers, etc., are certain solutions to help make informed decisions and avoid risks.
5. Track Freight Metrics
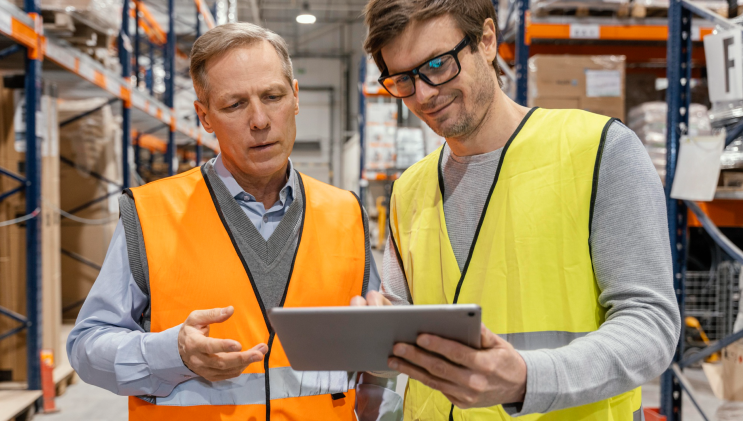
Manufacturers always strive to achieve dependability from customers to build a reputation. Retailers, on the other hand, are more inclined to deal with the right time and place for delivery.
Businesses have to partner with the freight carrier with a track record of consistent output. It is extremely important to match the supply chain and logistical demands with the freight carriers’ method of operation. A single incident of a late delivery can affect the entire supply chain. So, before choosing a freight carrier, it is crucial to evaluate the freight carrier based on specific requirement parameters or metrics. The following metrics should help –
Transit Time
Transit time is the entire delivery time span. It starts from the moment a product is dispatched from the seller till it reaches the customers.
Number of Stops & Average Stop Time
Multiple stops along the way of the delivery can jeopardize the entire process through unexpected delays. Also, long stop hours at different stopping points also delay the delivery time, ruining the reputation and disrupting the supply chain operations. Both the number of stops and average stop times need to be tracked and improved.
Average Time for Loading Freight
The average loading time for freight is the time needed to load a carrier with the freight. This time also includes the time to complete the paperwork simultaneously. It is an important metric for supply chain efficiency.
Route Optimization
Route optimization for the shipment is crucial for better logistics operations. Route-related costs for shipment are directly related to supply chain costs. So, route optimization can help make supply chain operations cost-efficient. Businesses with their own fleet have better route visibility and can easily monitor and improve the metric. For third-party carriers, the cost charged for shipping should provide insights into the routes.
Maintenance Schedule
A freight carrier that has a consistent maintenance schedule is not prone to breaking down. This is one of the things that keeps the supply chain from being disrupted.
6. Logistics Contingency Plan
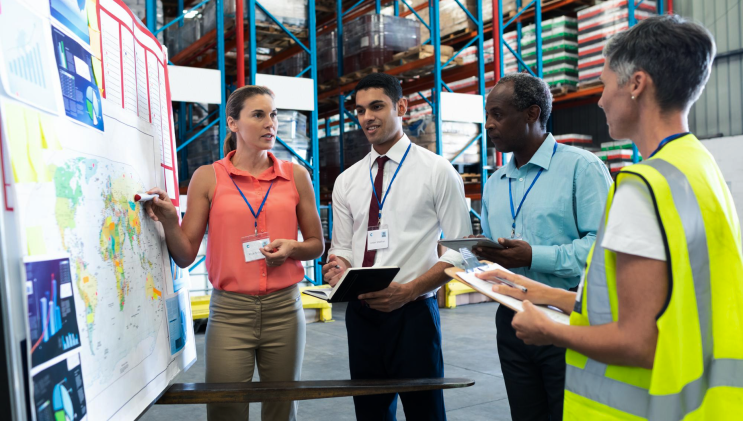
It is crucial to build and maintain a logistics contingency plan. Even in the face of supply chain disruption, a contingency plan helps keep the business operational. After COVID-19, the need for any contingency plan has become essential to logistics operations. Environmental effects like a pandemic can massively influence and disrupt the supply chain, which is why one or multiple logistics contingency plans are necessary.
Here are a few tips to follow –
- The first step is to map the entire supply chain and find the vulnerable points.
- Risk assessment of suppliers according to parameters such as geopolitical risks, economic risks, etc.
- Diversify the network of suppliers from different places and locations to mitigate supply risk.
- Logistics providers should be audited according to disaster plans.
- There should be a crisis response team to make critical decisions during an emergency.
- Strong communication channels should be in place to help properly manage information and instructions.
- There should be a minutely detailed document related to the contingency plan for the members to follow easily.
- The contingency plan should be dynamic and undergo necessary modifications as new scenarios and situations emerge.
- Create plan B, or more, as per the complexity of the supply chain.
7. Risk Awareness Training
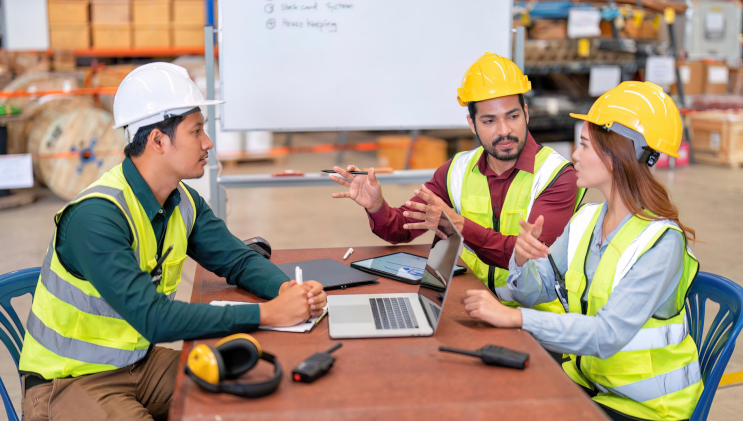
Large supply chains and logistics companies need training curriculums tailored for training employees. There should be detailed training schedules for risk awareness and precautions to take.
8. Constant Monitoring of Risks
An important strategy for risk mitigation in supply chain and logistics is through an effective risk mitigation framework. However, many businesses build a risk mitigation framework and are done with it. Proper risk mitigation requires constant monitoring. Digitized retail solutions can automate monitoring at different phases of the supply chain.
9. Data-driven modeling or Risk Scenarios
It is possible to use data science, data modeling, and predictive analysis to imagine and visualize scenarios of supply chain risks. Visualization of potential risk event scenes helps build better contingency plans or improve them accordingly.
10. Data Consolidation for Ease of Access
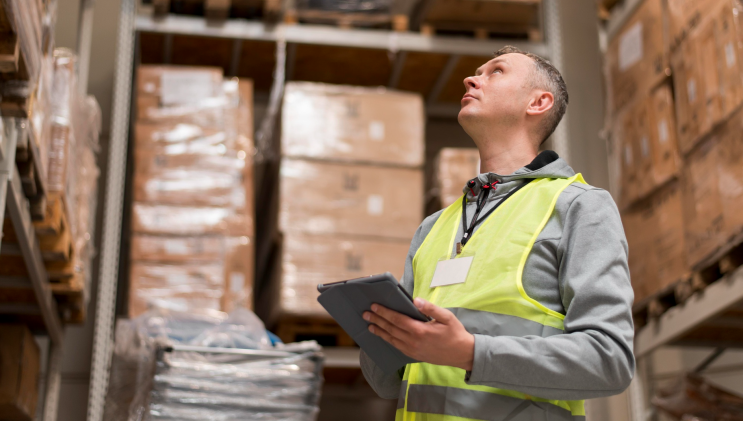
When a business deals with potential risks on multiple fronts, it may have different solutions and contingency plans. So, instead of keeping all the solutions in different data storages, it is critical to use one centralized data repository for better access to data. It also helps leverage data science and analysis to their best potential.
Impact of Risk Management on US Shipping Companies
Here are a few examples of USA companies that have done well using efficient risk management strategies for the supply chain.
Case Study 1 – IKEA
The famous retailer of home furnishing company IKEA has exposed itself to a large base of customers and audiences. They have 471 stores across 63 countries worldwide. However, despite its large span and almost 9500 product offerings in all the stores, IKEA has been able to maintain its stock perfectly at all times. On top of that, they have always been keeping the product price affordable for buyers.
But how?
They have their Supply chain risk management to thank for that. Here’s the secret to IKEA’s success –
- Firstly, they have a clear vision of what to offer to customers – they offer affordable, high-quality products.
- IKEA has always focused on the efficient production of high-quality products. A study reveals that 50% of IKEA furniture uses sustainable raw materials. In addition, using minimal materials helps IKEA lower transportation costs and use of human resources.
- They have always maintained a sustainable relationship with their suppliers. IKEA has more than 1800 suppliers across 50+ countries worldwide. Also, there are 42 trading offices that continuously maintain good relationships with the suppliers.
- Their management tactics foster competition among the suppliers, thereby keeping the level of their services consistent.
- IKEA has a manual for manufacturers to help reduce the environmental impact of their activities. They establish standard procedures to be followed through all of their business development activities. It affects all aspects of the supply chain in a positive way.
Case Study 2 – L’Oreal
François-Régis Le Tourneau, the Standards & Prospective Process Improvement lead for L’Oreal, has been managing his operations to improve the company’s supply chain better. L’Oreal has been the winner of Supply Chain to Admire in a row, and here are some reasons behind their success in the supply chain and logistics –
- First of all, they use a customer-centric agile supply chain to meet the needs of their customers on time.
- They have been heavily digitizing their sales initiatives, resulting in 40% sales through their eCommerce platform in China. In fact, they have reported a 34% sales increase globally.
- L’Oreal implements customer sentiment in its strategy to retain its customers.
- They have partnered with FuturMaster for two decades for demand forecasting, and it has only led to better results. Their dynamic forecasting process keeps L’Oreal at the top while inspiring other companies to improve their customer services.
- L’oreal uses advanced analytics, historical information, and automatic robotic solutions to manage its inventory efficiently.
- They use a robust supply chain strategy and synchronize their operations, raw material sourcing, and delivery of finished goods.
Case Study 3 – McDonald’s
McDonald’s has made sustainability-driven efforts to revolutionize all parts of its operations. They source their raw materials, food, and packaging, all through sustainable means. A better example would be its use of the “three-legged stool” philosophy. It allows McDonald’s to synchronize its franchisees, employees, and suppliers.
Here is how they do it –
- Vertical integration in the 1990s was one of the key aspects of the company’s success in supply chain management. McDonald’s has vertically integrated their supply chain since the 1990s. The company has ownership over more of its supply chain elements.
- They use (Just-in-time) JIT for eliminating cost and reducing waste.
- Also, McDonald’s ensures strict temperature and time control throughout the production process and ensures employee training for quality control.
- McDonald’s has a huge chain of restaurants and food suppliers who create and uphold the company values.
Final Words
With proper risk management strategies for logistics and shipping, businesses can improve their operational efficiency, cost management, environmental sustainability, and supply chain continuity. Various supply chain management and logistics companies provide BPR (Business Process Reengineering) to eliminate waste, shorten lead times, and reduce duplication of work.
The use of technology, forecasting, and integration of AI has also been revolutionizing the supply chain industry. As the types of risks in the supply chain keep evolving, so do the strategies. Hopefully, this article provided you with some valuable knowledge. Connect with us for further queries that you want to answer.
For More Smart Business Ideas Click Below!!
Comments Are Closed For This Article