3 Key Indicators That Show It Is Time To Standardize Your Business Processes
5 Mins Read
Published on: 21 January 2022
Last Updated on: 24 January 2022
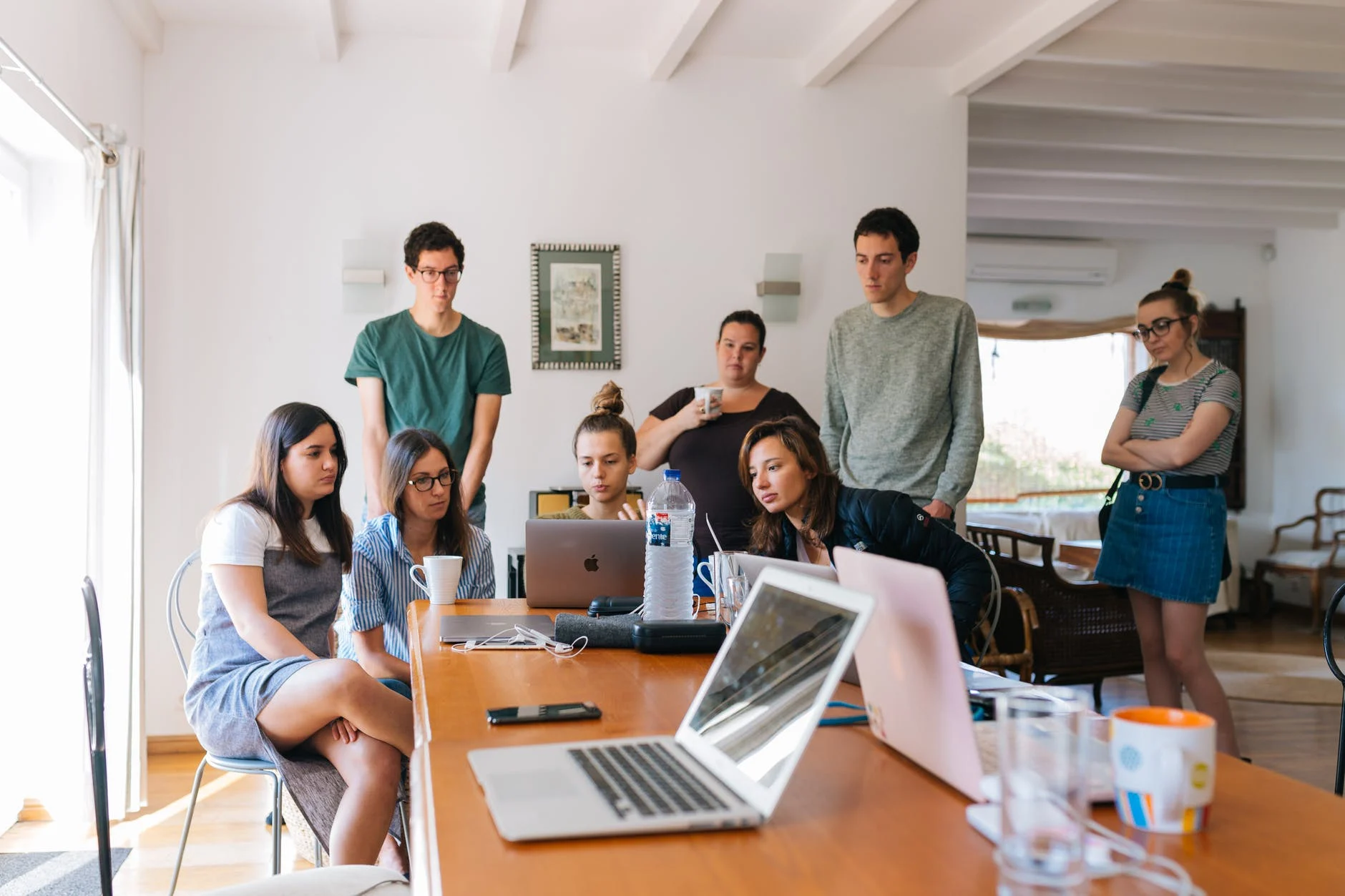
toc impalement
Sound business processes are instrumental in improving the business productivity and success of any venture. The strategic vision and goals of any business can be achieved only with the strong foundation provided by stable business processes. Your business processes are what turns raw materials and capital into useful goods and services.
For a business to run like a well-oiled machine, standard business processes have to be in place. The processes should not undergo any disturbance with change in personnel or environmental circumstances. Standard processes also help in the synchronization of activities across branches in different geographical locations.
First Business Processes Standardization Is A Brain Child Of Henry Ford
A well-known example of business process standardization comes from Henry Ford, the innovator of assembly lines in factories. Though the meatpacking industry widely used assembly lines, it was not widely used in other industries. Henry Ford identified this innovation, improved on it, and implemented it in Ford automobile production.
His apocryphal quote, “A customer can have a car painted any color he wants as long as it’s black,” is a testament to the standardization in the Ford assembly line. The Ford motor cars of the era did not provide any frills to customers. This helped them scale their operations at a very low cost. This, in turn, helped them sell vehicles to customers at an attractive price.
While the benefits of process standardization are quite obvious, many businesses fail to recognize its power. The failure to implement process standardization is reflected in the various measures of business outcomes.
Rise In Faults And Failures
Failure of machines and processes disrupt business operations. Some faults are unavoidable. No matter how optimized the business processes are, occasional faults are inevitable.
But having regular failures is unacceptable. Frequent outages and downtimes indicate problems that run deep in the organization. Occasional faults and failures are just manifestations of unresolved, hidden problems. Each industry will have a different quantum of failures associated with it. While analyzing them, you should compare the failure rate with peers in the industry.
One of the most common reasons for failure is the absence of standard operating procedures (SOP) for your business processes. The ambiguity without SOPs will cause errors from operators, which eventually cascade to widespread failure.
Non-adherence to existing SOPs could also cause failures. Business managers have to keep an eye out for failure rates within the organization. Rising rates of failure indicate some business processes need to be standardized. Managers have to perform root cause analysis to pinpoint the reasons for failure. The findings should be used to standardize processes to avoid future failures.
Stretched Working Capital Cycle (WCC)
Working Capital Cycle (WCC) is a purely financial metric obtained from the financial statements of a business. But it is an excellent indicator of the efficiency of business operations. The formula for calculating WCC is as follows.
Working Capital Cycle in Days = Inventory Days + Receivable Days – Payable Days
WCC indicates the efficiency with which the working capital of the firm is converted to cash. Crudely speaking, WCC is the time taken from paying for raw material to getting paid for finished goods. Increasing WCC means your business processes involved are inefficient.
More often than not, financial data indicates where the process is sub-optimal. When WCC is increasing, you need to identify the reasons for the same. Cues taken from financial statements have to be investigated to pinpoint the reason for the deteriorating WCC.
The three main parts affecting WCC are:
- Time is taken to collect outstanding invoices from customers
- Time in which the suppliers have to be paid
- Time is taken to convert raw materials to finished goods.
Improving and standardizing the processes around these three elements will improve WCC.
Increasing lead time
Lead time is the time taken from the start of a process till the process is completed. Each process in a business has standard lead times. The complete production process can be broken down into various sequential processes that have individual lead times. Constantly monitor the lead times for each of your business processes and sub-processes.
When the lead times for the processes keep increasing, it indicates inefficiency in the process. The cause for the inefficiency will be different in different instances. Identify the reasons for each inefficient process. The first investigation has to be on whether inefficient processes are due to non-standard operating procedures. Standardizing processes will bring down lead times and increase efficiency.
How to improve?
The indicators mentioned in the previous sections demonstrate a lack of standardization in business processes. Constantly track the different metrics to understand the efficacy of processes in your business. Once a deterioration in metrics is detected, the primary reasons for the same have to be investigated. Perform root-cause analysis to pinpoint the core reasons for process deterioration.
Once the root causes have been identified, fixing them would be straightforward. In most instances, process deterioration is due to non-standard business practices. Some of the common ways to standardize processes are listed below.
- SOP: Formulate standard operating procedures for each process. This ensures that all operators and employees perform tasks to the same standards.
- Checklist: Checklists are powerful tools for the easy implementation of SOPs. They secure process adherence on a wider scale.
- Employee training: Employee participation is paramount in implementing standard business processes. Provide adequate training to the employees regarding the use of SOPs and checklists.
- Process automation: Automating your business processes helps to standardize the operation. With that, processes become algorithmically implementable, and there will be no deviations from the codified procedural steps.
- Maintenance automation: Even when businesses automate their processes, they overlook maintenance. Maintenance at the right time is essential for smooth operations. A CMMS solution should be used to automate all maintenance activities.
Standardize processes for business success
Standardizing business processes is required for efficient operations. Due to myriad reasons, businesses falter at that. This article discussed three leading indicators that can be used to identify process deterioration due to non-standard business processes. The only way to fix and improve business operations is to standardize and automate them.
This helps to gain the most from the assets of your business processes. Standard processes also help to cut down costs and improve profitability. Keep an eye out for business process deterioration, identify the root causes for those, and eliminate such instances with standardization.
Founder Bryan Christiansen is the CEO of Limble CMMS. Limble is intelligent, user-friendly mobile CMMS software. This software is minimizing the efforts of all the maintenance-related hazards. Turn your maintenance into an automatic by simply streaming the whole operation.
Read Also:
Comments Are Closed For This Article