Natural Disaster Preparedness In US Logistics: Mitigating Supply Chain Disruptions
6 Mins Read
Published on: 16 March 2024
Last Updated on: 10 September 2024
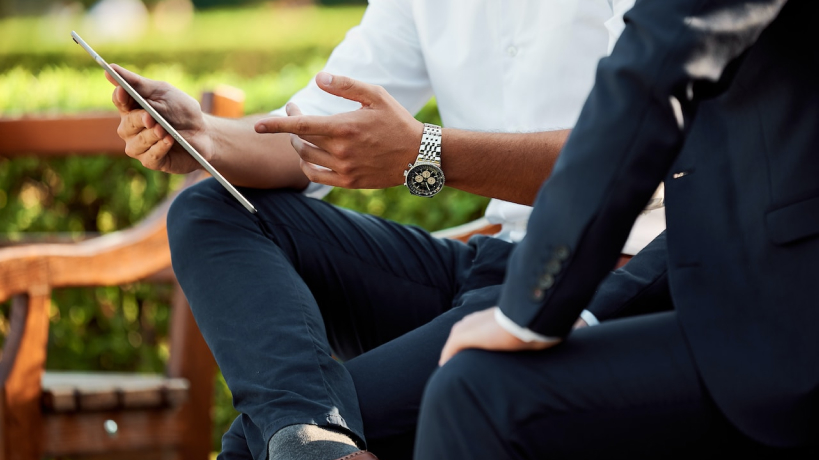
toc impalement
Supply chain disruptions have become common in the last few years, especially after the global pandemic and subsequent international conflicts. Furthermore, labor shortages, cyberattacks, bottlenecks in transportation, natural disasters, and economic turmoil can add more to such disruptions. Hence, organizations are intent on investing in contingency planning and improving their supply chains with new technology.
In addition to that, with unpredictable market demand and economic fluctuations, fresh challenges in supply chains are on the rise. In this article, you will learn about the issue of supply chain disruptions in US logistics. This article also shows you various ways to mitigate supply chain disruptions if you depend on US logistics. Hence, to learn more, read on through to the end of the article.
US Logistics and the Issue of Supply Chain Disruptions: Major Causes
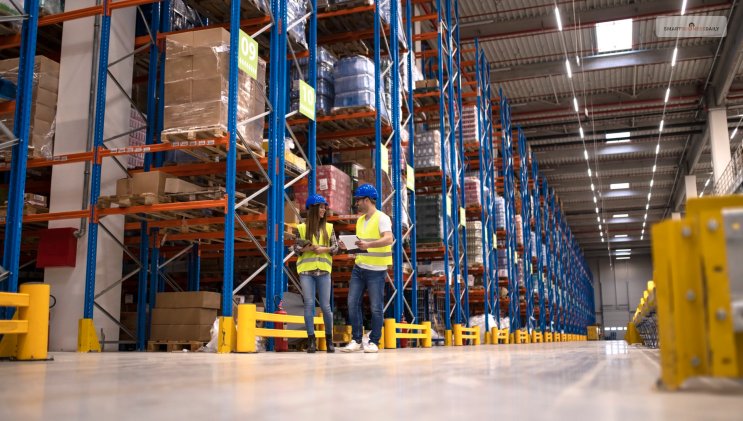
Basically, a supply chain consists of a network of people and companies who work together to manufacture and supply a product and deliver it to the end consumer. Any disruption in the supply chain can lead to interference in the production, distribution, and sales operations.
Supply chain disruptions can occur due to both internal and external problems. While internal problems can be resolved, dealing with external issues is difficult and challenging. Hence, businesses need to plan beforehand how they will deal with various supply chain problems.
With the rise of international conflicts and economic ups and downs, supply chain disruptions have become a common issue. Additionally, shortages in the supply chain are adding to the problems. Such challenges also test the flexibility, ingenuity, and resilience of supply chain leaders within organizations.
What is the Impact of Such Supply Chain Disruptions?
According to Netsuite.com,
“Supply chain problems can have a severe impact on businesses, often damaging their overall performance. To reduce risks and mitigate the impact of disruptions, companies may employ a variety of supply chain strategies, including preparing backup-supplier arrangements, geographically restructuring supply lines, and increasing inventory levels.”
Supply chain disruptions are the biggest threats to supply chain networks, as they interfere with the supply chain management processes. Furthermore, they cause big harm to businesses that are involved in the process. Apart from that, such disruptions can also slow down shipments, degrade the quality of products, increase the cost of the product, and can also damage brand reputation.
Hence, supply chain managers focus on improving supply chain strategies from time to time. The goal is not only to resist the current challenges but also to thrive in them. Furthermore, many investors, consumers, and governments also judge companies based on how they respond to supply chain disruptions.
Steps to Mitigate Supply Chain Disruptions in US Logistics
According to Accenture,
“Businesses must navigate disruption’s financial and operational challenges. And they need to do so while rapidly addressing the needs of their people, customers, and suppliers. With the right actions, supply chain leaders can turn massive complexity and disruption into meaningful change. Businesses need to create value chains with long-term resilience. This requires holistic approaches to managing the supply chain.”
The following are some of the major ways through which businesses can prepare for supply chain disruptions:
1. Assessing Risks and Vulnerability of Supply Chain Disruptions
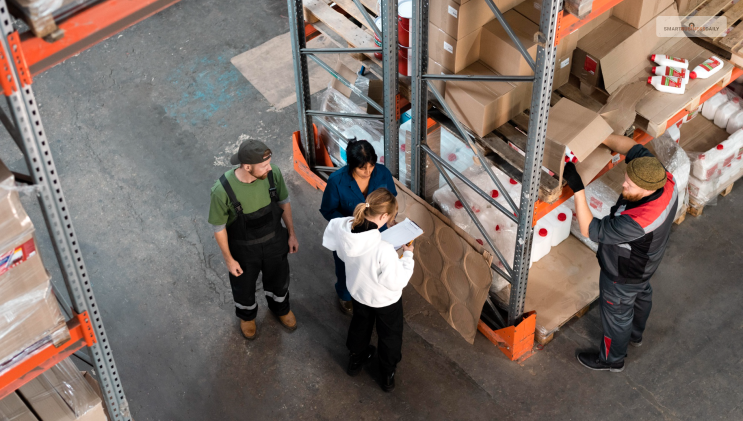
You must always expect the unexpected in your supply chain. However, it is better to have a good idea of various risks that might threaten the supply chain. Once you assess various risks and vulnerabilities of your supply chain, you can make it more resilient and flexible. Hence, you will be able to improve its performance for the better.
Here are a few things you can do in this case:
- Gather data and accumulate relevant details for a thorough evaluation. Make sure you have a clear idea of the system’s vulnerabilities.
- Focus on finding those risks that can have a devastating financial impact on the supply chain.
- Once you get a good grasp of potential risks, you can jot down strategies to minimize the effect of such risks.
2. Contingency Planning for Different Scenarios
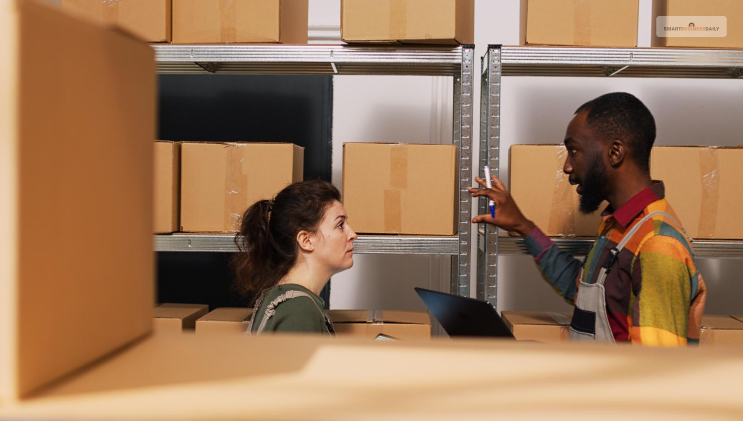
Oracle.com explains –
“Every company that relies on a supply chain needs to plan for worst-case scenarios. For example, companies can monitor their suppliers’ financial performance to gauge which ones are at most risk for going out of business and then reduce their dependence on those suppliers. Likewise, companies can reduce their reliance on suppliers in politically unstable countries.”
The most popular way to reduce the risk of supply chains is using the PPPR (Prevention, Preparedness, Response, and Recovery) model. Here, with the help of this model, you will be able to take steps towards avoiding risks.
Also, you will be able to create a contingency plan to reduce the impact of the disruption. This will enable you to ensure that the supply chain returns to its normal state soon. Furthermore, you will also be able to learn how to improve your supply chain management system.
3. Diversify Your Supply Chain to Reduce Redundancy
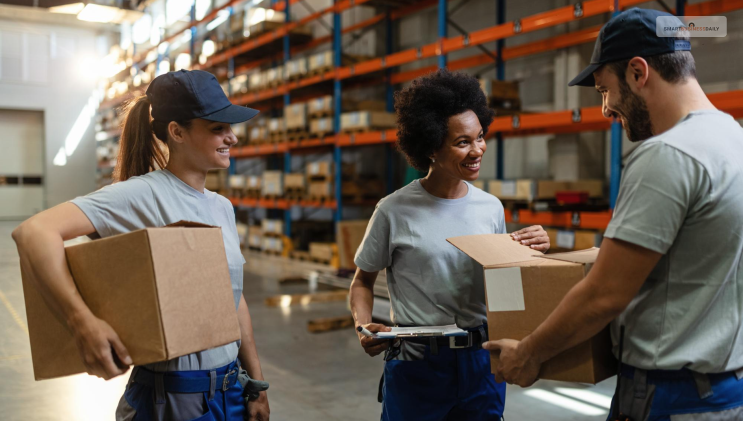
It can be risky if you depend on a single supplier to get supplies of products or raw materials. Here, if your supplier encounters a problem, it can disrupt the operations of your supply chain. Hence, it is essential to diversify your suppliers.
However, it is easier said than done since there is a risk of damaging supplier relationships. This holds true especially if you avail of the services of two or more competing suppliers. Hence, you will need to take steps carefully in this regard.
Apart from that, supplier diversification is essential since your supply chain also needs to adapt to changing customer demands. Hence, you will need to work on building relationships and learn to use creative communication and diplomacy to make the most of your suppliers.
4. Explore New Technology for Better Communication
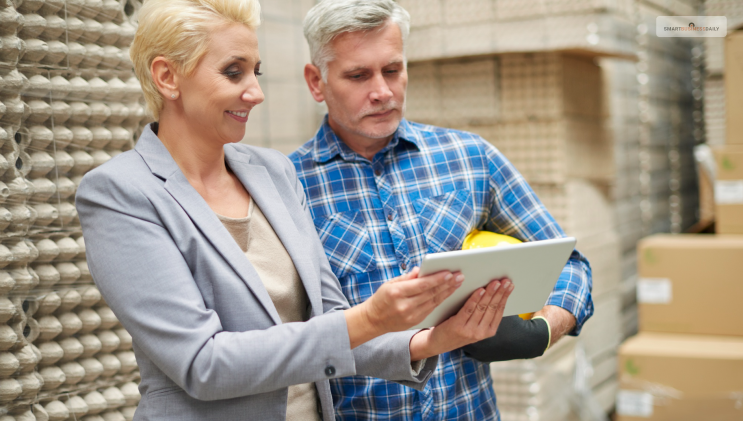
With the improvement of technology in your supply chain, you can ensure better visibility and communication. Also, you will have better access to data with better access to new forms of technology. Generally, the role of data in supply chain resilience is really big. Hence, how you deal with data as a part of supply chain management will make or break your supply chain network.
Furthermore, start leveraging AI for your supply chain and get access to real-time insights into data. This will help you make better decisions in case of sudden occurrences of risks and vulnerabilities. In addition to that, AI can also help you find loopholes in your system and predict future problems by analyzing data of previous disruptions.
5. Relationships are Key to Supply Chain Disruptions
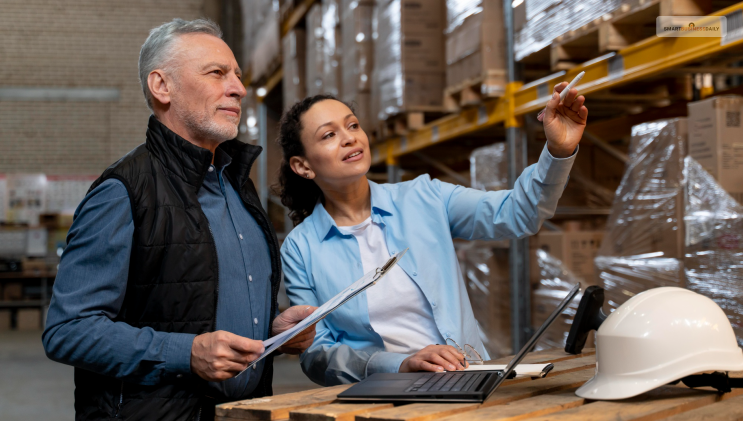
A great way to limit supply chain disruptions (apart from unavoidable ones) is to have better relationships with your supply chain partners. A great way to develop a good relationship with your supplier is to call the supplier monthly/quarterly to discuss problems and solutions.
Furthermore, you can also make use of automation to improve supplier relationships. For example, you can use a Supplier Relationship Management system that sends automatic notifications to suppliers in case of delays. This way, you can also ensure better communication and information transfer. All these factors can contribute significantly to limiting supply chain disruptions.
Generally, it is essential to set expectations and communicate with the suppliers beforehand. This will help establish a better flow of operations between you and your supplier. Moreover, you must also review them from time to time.
Wrapping Up
As supply chain disruptions have become common in recent times, it is essential for you to prepare for risk management beforehand. However, since every supply chain has its unique sets of requirements, it is essential to review all aspects before you think about making changes. Hence, plan accordingly.
What major supply chain disruptions do you think are common in US logistics? Consider sharing your thoughts in the comments section below.
Frequently Asked Questions!! (FAQs)
The following are some of the most frequently asked questions on supply chain disruptions:
Ans. Supply Chain Disruptions happen due to a disturbance in the production, sales, and delivery of products. This can occur due to a natural disaster, pandemics, regional conflicts, economic issues, etc.
Ans. Some of the major causes of supply chain disruptions include:
Natural Disasters
International Conflicts
Pandemics
Economic Issues
Ans. The following are the major impacts of the supply chain on business:
Delayed operations
Significant financial losses
Loss of sales or market share
Damaged brand reputation
Lack of customer satisfaction
Ans. Here are a few ways of dealing with Supply Chain Disruptions:
Assess the risks and vulnerabilities in the business
Prepare a contingency plan beforehand by thinking about different scenarios
Using the newest technology to have better visibility and communication
Diversifying supplier sources.
Building relationships with suppliers.
Ans. The following are some ways in which you can mitigate supply chain disruptions:
Using new technology
Gain better data insights and analyses from AI to make future predictions.
Diversification of the supply chain
Comments Are Closed For This Article