How To Introduce Automation Into Your Warehouse?
25 July 2024
6 Mins Read

toc impalement
Times are changing, and warehouses are racing to keep up. A range of economic pressures is making storage and fulfillment increasingly competitive, even as demand increases. This is why warehouse automation has become the need of the hour.
One of the ways warehouses are addressing this is the rapid uptake of automation, both to improve productivity and to make up for shortfalls in labor.
Any level of automation is a major change for a warehouse that’s never used it, however, and a bad implementation of automation can cause as many problems as it solves.
Here, then, is a basic guide on what to think about when introducing automation into your warehouse – from preparing the space to choosing the best kind of automation for you.
The Benefits Of Automation
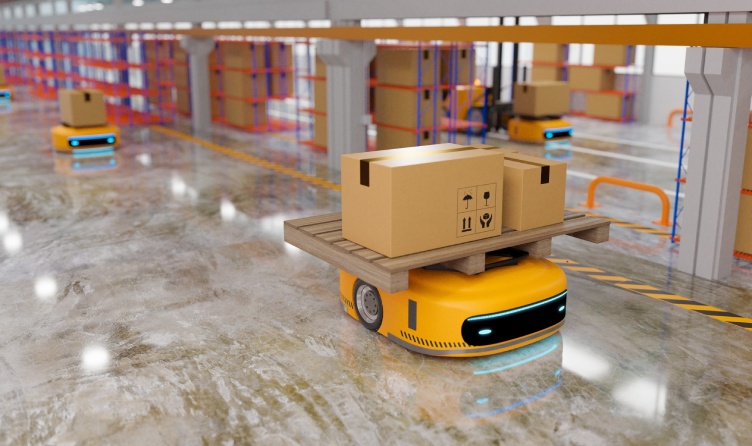
The past few years have seen greater visibility for advanced warehouse automation, ranging from picking robots to autonomous vehicles for transporting large items and pallets. Initially, the feeling from many industry observers was that automation was only of real concern to the biggest players in the market.
By far, the biggest investor and innovator in warehouse automation was Amazon, which obviously could afford to use the investment in advanced technologies.
However, the high costs and repeated delays to projects such as Amazon Prime Air seemed to demonstrate that major innovations were some time away and subject to a great deal of trial and error.
Automation, meanwhile, was seen as a way to reduce or eliminate the human component in its business – an area where it had already generated controversy for undervaluing employees. For smaller firms who already couldn’t compete with Amazon in terms of logistics, the issues that automation solved for Amazon seemed very alien.
What’s changed in the intervening years is both the advancement of automation and the realization that it can be more broadly and easily applied than was previously assumed.
Different kinds of automation can be applied to different parts of a warehouse – and the wider supply chain – in an ad-hoc manner or as part of one holistic system.
Thanks to rentable robots-as-a-service (RaaS), even smaller businesses are finding that autonomous vehicles and robots are accessible from a cost and integration perspective.
Integrating Warehouse Automation For Your Benefit
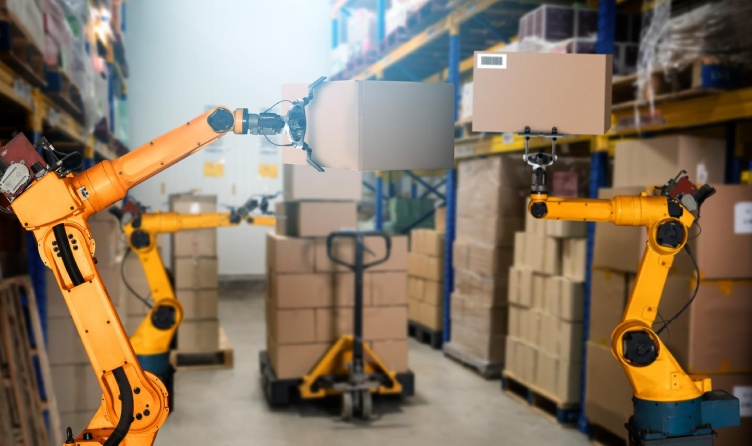
Adding some elements of automation to your warehouse is easier than it once was, largely thanks to the proliferation of different automation technologies. But this doesn’t mean that you can rush into it headfirst, thinking that robots will solve all your problems.
Buying or renting autonomous vehicles and robots should be seen much like hiring new employees: a process of pre-planning, rigorous investigation, and careful integration.
Establish Your Picking Process
It’s important to start by establishing exactly how your warehouse functions and the aspects of warehouse operation that you’re looking to augment or replace with automation. The most obvious is picking and the journey of items through the fulfillment process.
You may decide during this process that you don’t need automation, as the majority of warehouse tasks use methods such as piece picking that may not make sense for an autonomous vehicle.
Areas likely to benefit from automation would be batch or zonal picking, where the autonomous vehicle or robot can calculate an optimal route through an area and easily carry multiple items from a single order without having to detour.
Similarly, zonal picking or packing can be well-suited to new generations of robots that can grip objects more effectively and are ideally suited to repetitive tasks such as line work.
Storage and retrieval is also an ideal area for investment in automation. Guided, semi-autonomous vehicles and ‘cobots’ can ferry pallets around a warehouse, either storing and retrieving them from racks or delivering them to picking and packing stations.
There is also the longer-lived and more familiar automated storage and retrieval system (AS/RS), where a robot navigates up and along the rack face to pick up small items and bring them back.
Assess Your Warehouse Design
The next thing to think about is how the robots or autonomous vehicles will navigate your warehouse space. This is a useful thing to think about in terms of people as well as robots, and not something that every business does often enough.
If you can find an easy way to rearrange or improve your racking to make picking faster and easier, this may negate the need for automation altogether – or, at the very least, make it even more efficient.
Take an AS/RS, for instance. Its ability to scale racking allows it to navigate extremely narrow spaces between aisles, making it an ideal candidate for space-saving narrow aisle pallet racking.
Elsewhere, you may find that simply moving more commonly ordered SKUs nearer to packing stations speeds up retrieval times for human or robot operators. Adapting your racking to better store different pallets and item types can also make the picking face more accessible and speed up the picking process.
Traffic may be another consideration. While autonomous vehicles have advanced collision avoidance systems, wide-aisle racking may be seen as necessary to allow for the safe transit of vehicles and people in close proximity. Multi-tier racking may also be an option, isolating the autonomous vehicles or robots to one specific area.
An advanced warehouse management system (WMS) could even help optimize traffic flows by directing robots and personnel and speeding up picking up and storage. All of these aspects could inform both better overall warehouse design and better design to support autonomous vehicles.
Choose The Right Automation For You
Part of the reason that warehouse automation has become more practical is that there are now many types to choose from. As such, it’s important to get a full understanding of the options available to you and what best suits your business.
If you’re unsure about the benefits or costs of automation, a good initial step may be to introduce handheld terminals (HHTs). These can exchange information with a WMS, allowing you to automate inventory management and speed up picking for warehouse operatives.
A step up from this is automatic guided vehicles (AGVs). These semi-autonomous vehicles use a range of sensors to traverse simple routes through a warehouse and are best for low-traffic areas or times of day.
Autonomous Mobile Robots (AMRs) have more advanced obstacle detection and can use a range of positional data to change routes on the fly, working in coordination with a WMS.
Other examples don’t inhabit the warehouse floor at all. Automated sorting systems, conveyors, carousels, lifts, and other goods-to-person (GTP) systems can help expedite the travel of goods from storage to distribution and improve inventory management through accurate scanning.
More advanced mobile scanning devices meanwhile can use wireless sensors or even AR headsets to direct operatives on where to place and retrieve pallets or SKUs.
Integrate It Into Your Warehouse
We’ve mentioned the power of modern warehouse management systems and how they can help to drive automation by sending instructions and recording data.
The automation provider will usually be able to advise on the best way to integrate automation with your WMS, or which one to use. However, there are other things to consider when integrating automation with your warehouse – many of them far less technical.
One is how you intend to integrate the robots and vehicles with your existing workforce. While modern autonomous robots are extremely safe, operatives may still need training on how they operate and how to navigate the warehouse while they are moving around.
They will also likely need to know how to interact with the robots to load or unload pallets or hand off picked items. This is not to mention the staff who will be operating and overseeing the vehicles and WMS.
You’ll also want to assess the integration as it is happening and consult with employees to ensure that it proceeds smoothly. There will inevitably be some teething problems, whether those are issues with WMS integration, wireless dead zones, or robots misbehaving.
Employees should be free to provide feedback on how the integration is going, and adjustments should be made to ensure that the maximum value is being gained from your new additions.
Concluding Words
Automation won’t be helpful or necessary for every business, but warehouse automation is becoming an increasingly attractive option owing to staff shortages and economic pressures.
We hope this guide has given you a few ideas about how to integrate automation into your warehouse and reap the potential benefits.
For more information on modifying and installing warehouse pallet racking that gets the most out of AGVs, AMRs, and robots, get in touch with us today.
Additional Reading:
Comments Are Closed For This Article