How to Ensure Consistent Part Dimensions and Quality in CNC Machining
02 April 2025
5 Mins Read
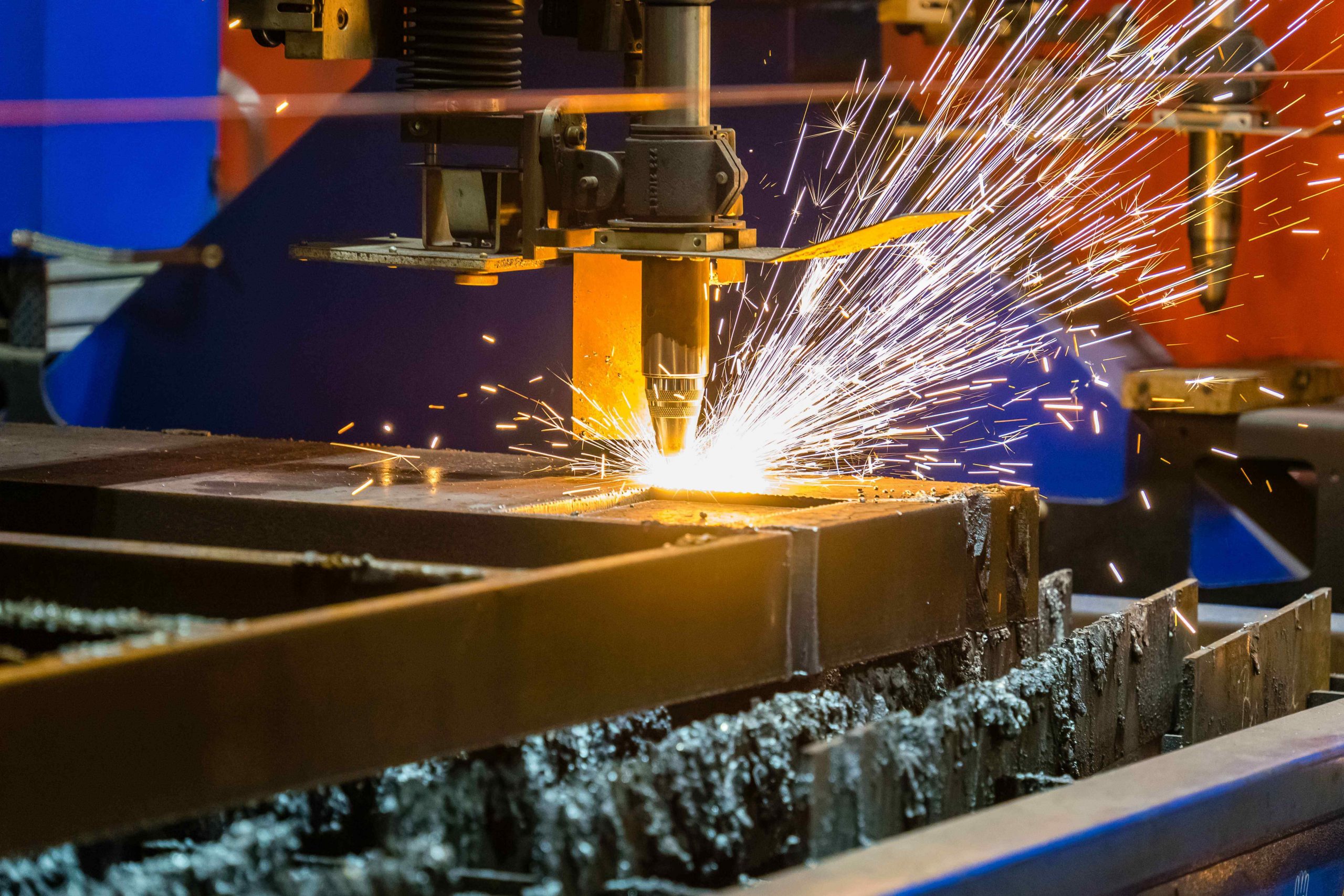
toc impalement
The accomplishment of consistent dimensions together with quality outputs in CNC machining processes demands thorough attention to equipment and processes alongside materials selection, such as machine setup and tool selection, alongside material properties and environmental conditions.
Faulty dimensions alongside poor quality standards result in expensive reprocessing along with production delays and have significant effects on dimensional accuracy and surface finish levels.
Manufacturers who prioritize preparation, optimize processes, and implement quality control procedures will obtain reliable outcomes while minimizing waste and meeting strict requirements.
CNC Machining: Everything You Have To Follow To Maintain Quality
The CNC machining process overcomes the limitations of manual control. No live operators are needed, and they do not have to command the tools via wheels, levers, and buttons.
However, you have to make sure of certain things to ensure proper calibration and quality of the products. Here is everything you should take care of.
Start with Proper Machine Setup and Calibration
The foundation of Consistent CNC machined parts originates from the machinery itself. A machine that needs calibration will make errors that worsen with time, leading to dimensional problems in the parts.
CNC machine functionality depends heavily on routine maintenance checks, which focus on accurate alignment among axes, true spindle accuracy, and low backlash values.
Parts shifted slightly off-center when the X-axis does not align properly and the lead screws develop too much backlash resulting in imperfect depths of cut.
Setting up CNC machining requires proper workpiece fixation together with the selection of suitable fixturing. The material has the potential to shift when insufficient clamping exists, which results in changing dimensions.
The workpiece stability can be achieved by using precision vises together with custom jigs and vacuum tables to keep CNC machined parts within their designed geometry.
Each operation requires verification of machine and tool offset settings before starting because this prevents errors from accumulating, which maintains operational accuracy.
Select the Right Tools and Parameters
The selection of tools together with machining parameters determines how precise CNC-machined parts will turn out.
Tools in substandard conditions alongside improper choice result in surface faults while creating manufacturing dimension problems in addition to breakdowns.
A dull end mill causes heat concentration, which leads to workpiece expansion, which modifies its dimensional accuracy.
High-helix end mills dedicated to aluminum, combined with coated carbide tools built for stainless steel, produce neat cutting results and minimize tool wear.
Three vital cutting parameters exist which include spindle speed and feed rate along with depth of cut.
The optimization process applies to the specific material that requires machining. The process of machining titanium becomes problematic at high speeds because it produces work hardening, which results in unacceptable dimensional variations.
The combination of manufacturer guidelines and CAM software to simulate cuts can help fine-tune settings, ensuring that CNC machined parts are produced with consistent precision across batches.
Control Material and Environmental Factors
Manufacturing consistency in CNC operations strongly depends on both the material’s properties and the surroundings where the cutting happens.
Changes in material composition, including variations of hardness or internal stresses, create modifications in machining material behavior.
The erratic grain structure within an aluminum batch causes imbalanced cutting forces, which negatively affect the dimensions of CNC machined parts.
Applying standard procedures involving the evaluation of desirable suppliers combined with pre-machining hardness tests enables risk management.
Temperature and humidity conditions in the environment affect the results produced by machining processes. The phenomenon of thermal expansion in machines and tools, as well as workpieces, because of temperature changes results in dimensional modifications.
The parts in an uncontrolled machine shop facility can experience minimal dimensional changes that correspond with daily temperature fluctuations.
A controlled facility environment at 20°C (68°F) combined with material acclimatization before machining operations leads to better consistency.
Coolant use during machining operations controls the production of heat, thus protecting CNC machined parts from damage.
Implement In-Process Monitoring and Quality Control
The achievement of consistent quality needs active monitoring systems to be implemented during machining operations.
The real-time detection systems consisting of tool wear sensors with vibration detectors actively identify problems before they influence part accuracy.
Rapidly rising vibration signals may signal that a tool has become dull or that the setup needs adjustment because such conditions can generate dimensional errors.
The installation of quick solutions to production process problems stops defective items from advancing through the manufacturing pipeline.
The organization must carry out thorough quality assurance checks as the final step after machining operations.
Part specifications are checked by using precision measurement tools that consist of coordinate measuring machines (CMM), calipers and surface profilometers. SPC helps manufacturers monitor their processes to detect any changes that impact allowed tolerances.
A machine requires calibration adjustment or tool replacement when part diameter progression occurs during production to ensure accuracy. The quality of CNC machined parts remains intact when operators conduct inspections at the beginning of the process.
Standardize Processes and Train Operators
The human factor stands as a major contributor to CNC machining variation. Consistency throughout a CNC production process becomes possible by adopting standardized work instructions alongside checklists.
Proper tool change procedures, when carried out correctly, will prevent dimensional errors caused by inaccurate tool offsets.
Operator training is equally crucial for maintaining precision. Experienced machinists develop the skills to interpret machine systems, adjust parameters, and troubleshoot issues promptly.
Training sessions must address the optimal practices related to setup configuration and selection of tools. Moreover, it needs to address quality control procedures, and adaptive control system operation.
Conclusion
The production of uniform parts with high quality through CNC machining requires a system that monitors all operational steps.
The result of dependable machinery output depends upon each step of machine setup and tool selection, together with material control, in-process monitoring, and operator training processes.
Through strategic implementation, manufacturers can reduce manufacturing mistakes while ensuring that every CNC machined part passes exact product quality requirements.
READ MORE: